MusicRadar Verdict
Spaun has taken an existing concept and worked its fevered imagination on it to produce a thoroughly 21st Century kit. And in this territory kits have to be a bit special to justify their price tags... bullseye.
Pros
- +
Super thin shells. Modern sizes. Powerful and resonant sound.
Cons
- -
Quirky finish might not suit everyone.
MusicRadar's got your back
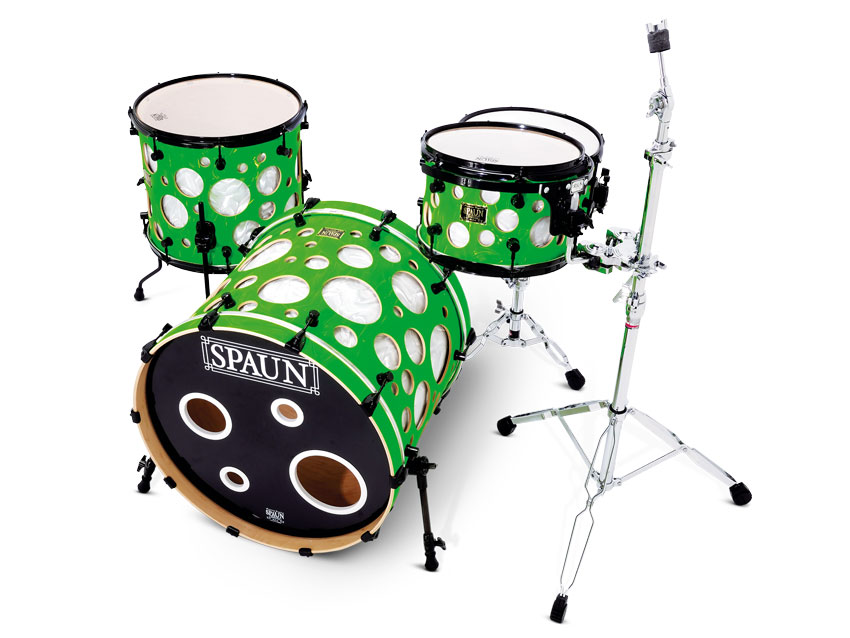
Spaun Edgevent Kit
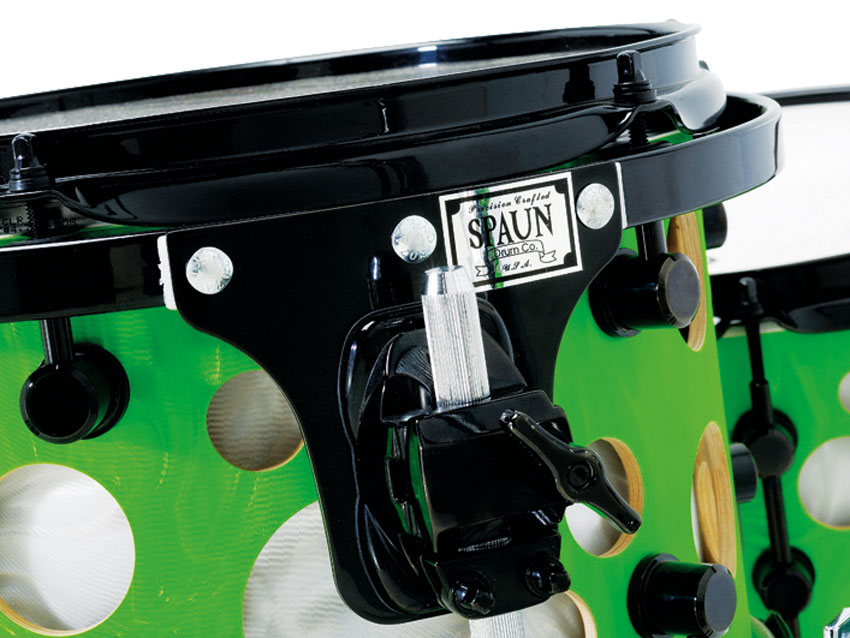
Spaun Edgevent Kit
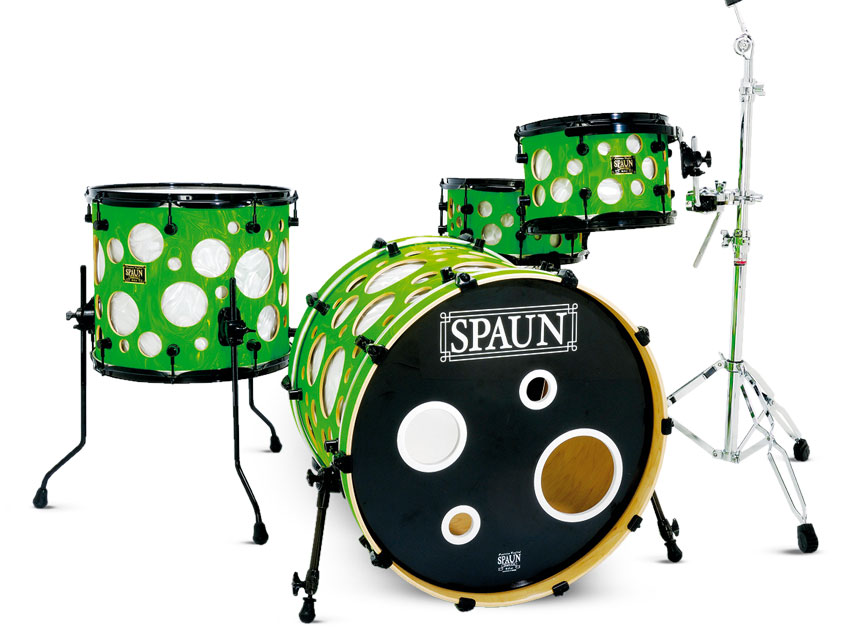
Spaun Edgevent Kit
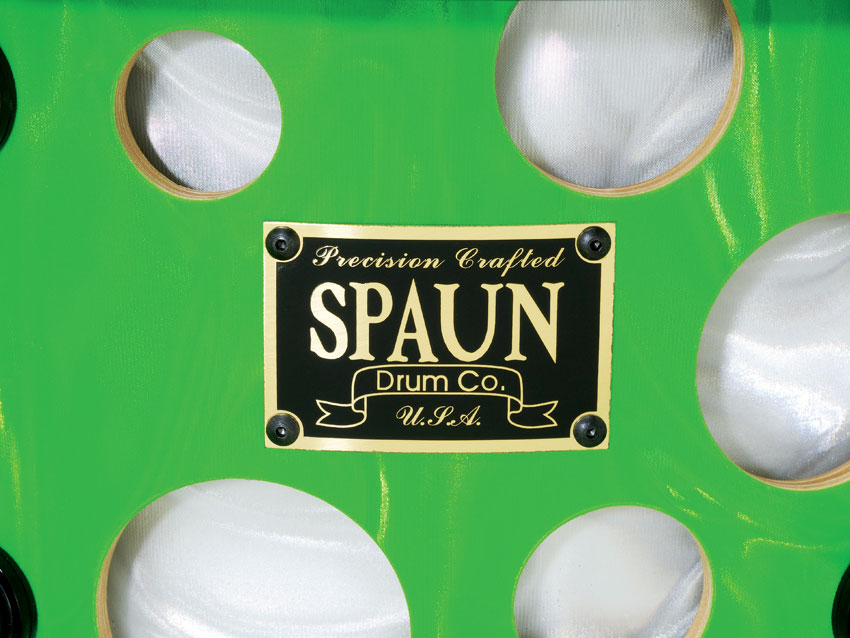
Spaun Edgevent Kit
Though Spaun is a relatively new brand in the UK, it's been in business for the past dozen years. If you know nothing else about Spaun, you're probably aware of its enthusiasm for attention-grabbing finishes. But beneath the imaginative lacquers and wraps sit high-end drums made with care.
A combination of a willingness to experiment and a need to produce ever more original finishes has resulted in the Edgevent kit, whose appearance can only be described as show-stopping.
Build
With a few notable exceptions, Spaun's wooden drums are generally made with thin (5.5mm) maple or birch shells cut with its symmetrical bearing edges. This all-maple Edgevent kit differs from regular Spaun drums as it revisits the shell-within-a-shell concept first devised in Britain by Alan Gilby and subsequently produced by Premier.
"The kick was reminiscent of one of those dance instrumentals where each hit from the bass drum momentarily obliterates everything else"
Drum shells resonate, producing sound and fixing lugs to them only stifles these properties. One solution is to make drums with two shells - an outer shell which holds all of the fittings and a second thinner shell inside, free of any kind of hardware, that can resonate unhindered.
The theory sounds straightforward enough, but putting it into practice involves some ingenious engineering solutions, more of which later. Let's deal with what's missing first...
It won't have escaped your notice that this kit is peppered with holes. This being a twin-shell kit, the holes are only on the outer shells. So, what are they doing there? Well, all drums require breathing holes in order to allow air movement when they're hit.
Normally, these are discreetly located in the centre of the shell, often within the manufacturer's badge. However, while working on prototype Edgevent drums, Spaun discovered that larger holes actually allowed this type of twin-shell drum to breathe more satisfactorily.
Want all the hottest music and gear news, reviews, deals, features and more, direct to your inbox? Sign up here.
The original Edgevent snares, introduced in 2005, featured uniformly-sized holes placed evenly around the outer shell, but they were a sober sight in comparison with the number and size of holes found here.
I can't imagine that the holes are all there for sound benefit. After a certain point, cutting more holes can't make any more difference, but they do make for an outrageous appearance. The name of the holes - Swiss Cheese Vents - reveals their inspiration.
Creating the holes is a slow and laborious process, with a single misjudgement having the potential to ruin an entire shell. Each hole is cut and sanded by hand after the wrap, in this case Green Swirl, has been applied. Currently, Swiss Cheese Vent drums are only available in wrapped or satin lacquer finishes. Spaun says it would consider making an Edgevent kit like this in a high-gloss lacquer, but it would have to be by negotiation.
Any concerns about the strength of such heavily perforated shells were, in my time with the kit, unfounded. The cylinder is an incredibly strong shape - that's why underground tunnels are invariably dug in this shape - and the shells feel quite rigid.
Another useful payoff of drilling the shells out is the weight loss. Double-shelled drums are normally quite heavy on account of the extra wood used. The Edgevent drums, while not as light as single-shell equivalents, weigh less than you'd expect.
When it came to the inner shells, Spaun was unwilling to comment on many aspects due to fears that designs could be plagiarised. Without wishing to contribute to its worries, it's our duty to describe what we found.
Most twin-shell drums have reinforcement rings glued to the top and bottom of the outer shells. The strengthening properties are not really required; they're there in order to grip the inner shell and maintain a gap between the two shells.
The Edgevent design isn't a million miles away from this, but there are crucial differences. The reinforcement rings - if that's what they were originally intended to be - are divided into segments running around the inner circumference of the outer shell. The vents that separate each portion of ring were devised because Spaun thought that without them the drums sounded choked.
It's from these edge vents that the drums get their name. Such an involved piece of design suggests a significant effect on the sound.
In each drum the inner shell, which is wrapped in contrasting White Swirl, is sprung between the two sets of Edgevent ring. While the outer shells are eight-ply maple and .5mm thick, the inner shells vary in ply and thickness, but are generally thinner (in some drums as slender as 3.5mm).
Spaun's double 45 degree bearing edges (ie an equal angle either side) are cut on the outer shells. From the bearing edges the shells rake down across the Edgevent rings to the inner shells.
Hands on
This Spaun kit is made up of a 22"x18" kick drum, 13"x 6½" snare, 12"x8" tom and 16"x14" floor tom. The extra-thin inner shells point to a deep, dark response and the moment we attached a pedal to the kick drum a thunderclap of sub-frequencies ensued, making the wooden stage we were on vibrate in sympathy.
What could be discerned of the note was murderously low and drenched in warmth. The kick was reminiscent of one of those dance instrumentals where each hit from the bass drum momentarily obliterates everything else. An Evans EMAD batter fitted with a single foam ring ensured a clean response with near-perfect decay.
The toms gave similar performances to the bass drum delivering fat, powerful tones that mainly registered at the deeper end of the spectrum. Despite the prevalence of low-end, the toms had an aggressive edge, which enabled them to cut through rather than end up as muffled thuds within the mix.
The snare was every bit as impressive as the rest of the kit. It produced everything from a tight snap at the edges to thick backbeats in the centre. The darkness of the wood shone through, adding warmth to the unquestionable power. Rimshots were delivered with metallic precision, while at the other end of the dynamic scale the drum proved highly sensitive, responding to the smallest flick of a brush.