“When it comes to building guitar necks, there’s a quick way to do things and there’s a right way to do things”: Ever wondered how PRS makes its necks? This video walks you through a process where every detail matters
This behind the scenes video shot from the factory floor at PRS's factory in Maryland documents a meticulous build process in which there are no shortcuts
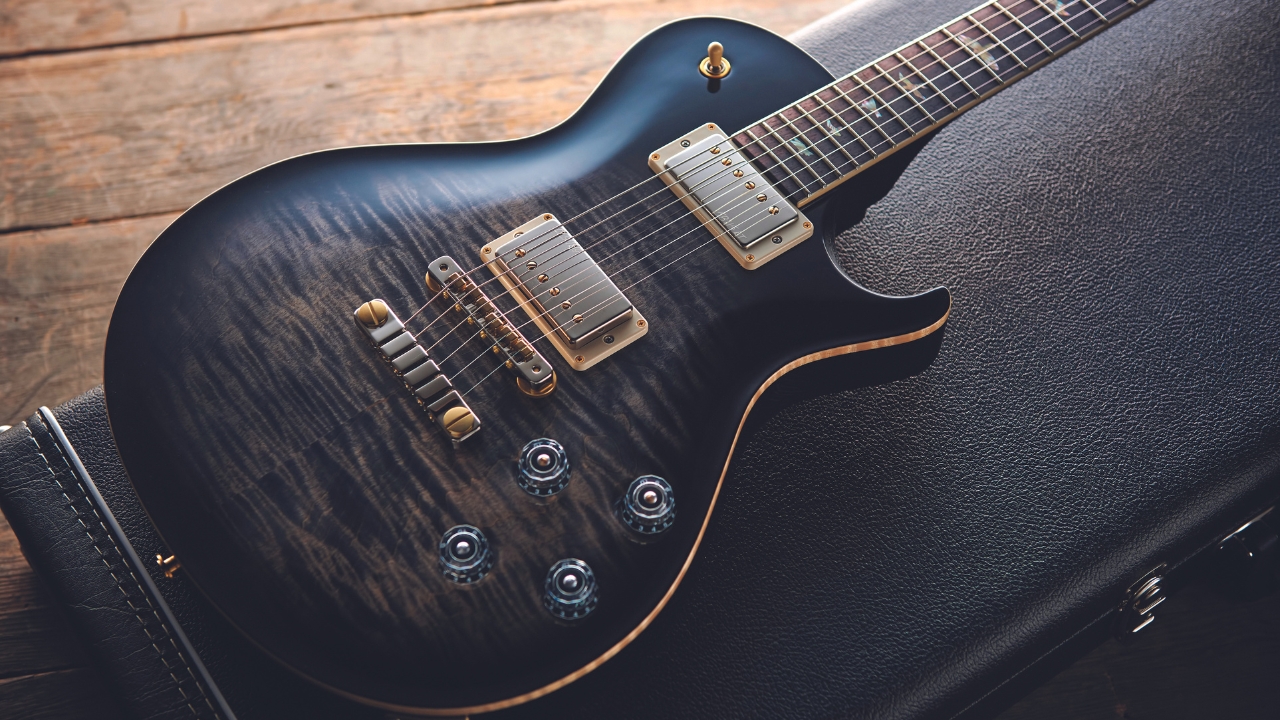
Ask any tech, any pro player, what makes a PRS a special electric guitar and they might tell you it’s the build quality, the tone, the feel or any of the usual metrics. But maybe the one thing that makes PRS guitars perform so consistently well is time – the time it takes to get all those details just right.
The brand has just shot a video for its From The Factory Floor series that offers a comprehensive look into the processes that go into making the necks for each of the guitars in the Core lineup. It is remarkable the work that is involved, and ultimately the time that it takes to put one of these together.
If you have ever wondered where your money goes on a high-end electric guitar, here is part of the answer. With second shift wood shop manager, Ryan Whaley, as our guide, the video takes us behind the scenes at the PRS factory in Stevensville, Maryland, where there are no shortcuts.
“When it comes to building guitar necks, there’s a quick way to do things and there’s a right way to do things,” says Whaley. “Here at PRS, quality has always been our driving force, so you know we do things the right way.”
So what does the right way involve? First off, wood, and lots of it. The first stage is to get the wood and cut it down into a neck blank size – “a giant plank of wood” – and then these are left to sit in the hot room for a number of days, before being prepared on the factory floor for the CNC machines.
A relief cut is marked out on the blank that will later turn out to be the “ears” of the neck, which are those wings on either side of the headstock that give it that recognisable PRS profile. Spotting details such as wood grain and colour are crucial to have a good match for the ear and neck blanks.
Another resting period in a hot room is required before it can be sent to the first stage of CNC machining process, when the truss rod channels will be routed into the neck. How long the neck blank spends in the hot room all depends on the species of wood. Whaley says you can’t hurry this stage of the process because it pays off in the finished instrument.
Want all the hottest music and gear news, reviews, deals, features and more, direct to your inbox? Sign up here.
“The bake and dry times are very important,” he says. “That way, once the guitar is finished and customer has it, all the moisture is out of the neck and that neck is completely stable, so you don’t have to worry about your neck moving on you right after getting your guitar.”
After the first stage of CNC machining, the truss rods are installed, then for assembling those necks with their ears, when it really begins to look like a PRS neck, and yet we are not even halfway through the build.
The fingerboard is yet to be glued on and levelled. There are further rounds of CNC. We also need frets on the ‘board. The headstock needs a veneer. There is sanding, so much sanding. That’s how Whaley started out at the company, sanding necks, over 13 years ago now. And there is a lot of checking.
“We’re checking and double checking at every stage to ensure that we sending forward only our best,” says Whaley.
If you want even more behind the scenes access and just happen to be passing through Maryland, remember PRS are now offering factory tours again after a few years’ hiatus. They cost just five bucks and last for around 90 minutes.
“People say it’s like going to Wonka’s candy factory,” said Paul Reed Smith. “I’m not sure about that, but there is nothing like talking to someone right after they’ve had a tour. You can see the lightbulb turn on while they are here – it really gives a full picture of all the care each employee here puts into their work.”
See PRS Guitars for more details.
Jonathan Horsley has been writing about guitars and guitar culture since 2005, playing them since 1990, and regularly contributes to MusicRadar, Total Guitar and Guitar World. He uses Jazz III nylon picks, 10s during the week, 9s at the weekend, and shamefully still struggles with rhythm figure one of Van Halen’s Panama.