MusicRadar Verdict
As a drummer himself, Sam Buckland has definite ideas about what constitutes a good drum. If his theories are bold, then his execution is doubly so - these are immaculately built drums. The designs are well-argued and the level of craftsmanship is absolutely outstanding. Spending this sort of money on a kit brings with it certain risks, not least keeping the drums safe and in one piece.
Pros
- +
These are beautifully built, handmade drums that really are one-offs.
Cons
- -
The drums are pretty heavy, and it’s a lot of money’s worth to cart around.
MusicRadar's got your back
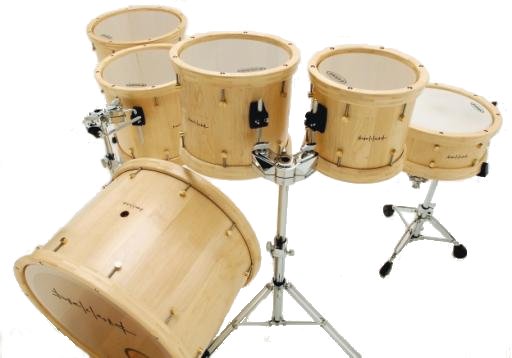
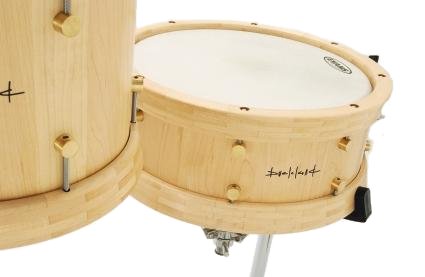
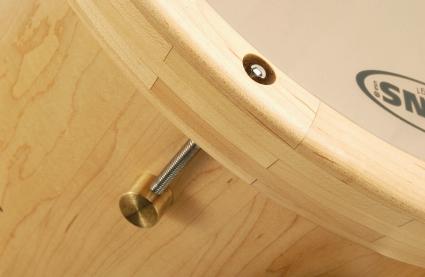
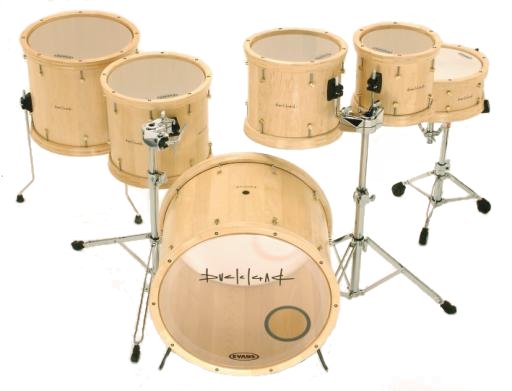
Newcomers to the art of drumming are well served by an array of manufacturers competing to offer a better value package. It has never been easier or cheaper to take up the drums.
As a player, you may well reach a point where your confidence behind the drum kit is matched by a desire to upgrade to a set of drums as serious and individual as yourself. In which case, you will find yourself entering a cottage industry of tiny companies, employing a handful of expert craftsmen. It is this small volume, high quality, bespoke end of the industry that Sam Buckland occupies.
Bucking the trend
To describe Sam as a new recruit to the ranks of drumsmiths would be a misnomer, as a lifetime´s work has gone into these drums. He began making his first drums 10 years ago and it is only now that he has actually put them onto the market. Sam is a drummer of some repute and has been a constant thread throughout the design and development of his drums.
Based in Shropshire, Sam is the son of a wood turner so has been surrounded by wood from an early age. He is as much a scientist as he is a craftsman and every aspect of his drums has a solid design reason for existing. Sam graduated from university with a degree in Audio Music Technology and has applied the knowledge to his drums. And when we say ‘his´ drums we really do mean ‘his´ drums. The workforce at Buckland Drums consists of just one person - Sam himself.
Each drum has been handmade by Sam. In my book that rates as a personal service. The bass drum alone is made up of 230 separate pieces of maple. Sam is fairly dismissive of mainstream manufacturers, reckoning that more time and energy is spent marketing drums than innovating. His approach to drum making incorporates design fundamentals and a profound understanding of wood.
This particular kit was made for Billy Cobham to use at a drum clinic in Shrewsbury, and took three months to design and build. The kit is large - all the toms are wide as they are deep - and heavy due to the amount of wood that has gone into it. Block shells are Sam´s preferred method of construction and each shell is 15mm thick.
A chip off the old block…
Sam is unswayed by arguments over whether the thickness of the shell influences resonance and volume. In his opinion, the sound of a drum is largely shaped by the sharpness and roundness of the bearing edges. Another key factor is the air loading - how the air in the drum affects the movement of the heads. Accordingly, these shells are completely smooth inside and unencumbered with any hardware or fittings, allowing sound to move freely between heads.
By their nature block shells are a good deal thicker than ply shells and so possess the depth and strength to support hardware without interrupting the inner space. In terms of both function and aesthetics this is exactly what Sam intended.
"The tuning rods are one of the few elements that have been bought in and they fit smoothly into the lugs. The drum key ends of the rods are harboured snugly within the wooden hoops. Cut and assembled by hand, they are made up of as many as 100 separate blocks of wood".
The shells are formed from maple (other woods are available) from a sustainable source. The blocks are an inch thick when first glued together and are lathed into shape and sanded. Externally, they are beautifully worked and finished with a light water-based lacquer and a clear wax. The bearing edges are hand-turned by Sam.
The bearing edge profile is of Sam´s own specification and differs from most drums in that it is angled entirely from the outside, leaving a perfectly vertical interior shell. The thickness of the shells means the counterhoop of the head fits flush with the shell. The curve from the bearing edge to the outer edge of the shell that supports the hoop is quite exquisite.
The lugs are again fashioned by Sam from 16mm solid brass bars. Drill holes 12mm deep are made in the 15mm thick shells and the lugs are then bonded into place. Sam´s designs generally incorporate one lug per three staves of shell and these drums all adhere to this rule.
Cock-a-hoop
The tuning rods are one of the few elements that have been bought in and they fit smoothly into the lugs. The drum key ends of the rods are harboured snugly within the wooden hoops. Cut and assembled by hand, they are made up of as many as 100 separate blocks of wood.
Once glued together, a pair of hoops requires half a day´s turning on the lathe. They are fantastically made - frequent rimshots left no impression. The design also means that there are no claws on the bass drum, making for an uncommonly attractive kick.
Tom mounts from Gibraltar are fitted at nodal points directly onto the shells of the three toms. We were concerned as to whether the weight of the drums might lead to problems when hanging them, but the generic ball and socket holders supplied stood firm through two-and-a-half hours of playing. The floor tom legs are located in similar mounts which are likewise simply screwed into the shell.
The bass drum spurs are also clamped by Gibraltar mounts, and the tongue on the playing side for clamping a pedal to is made by Sam. A fabulously cool Nickelworks snare release is fitted to the snare, but Sam already has his own prototype brass and wood strainer.
Live test
You´d expect a kit so lovingly built and carrying this sort of price tag to sound good, but we were gobsmacked. The bass and snare drums were almost impossible to fault. The kick drum blasted out taut, bassy waves that sent ripples in all directions. Even in a marquee, where the sound can so easily float away, the drum sounded huge, thumping clods of bottom-end out on demand.
The snare was everything that a snare drum should be, biting with the authority of a metal drum with woody warmth behind it. A tickle was enough to bring it to life, and it then sang all the way through the velocities. The word ‘pure´ is perhaps the only word that does the toms justice.
As with the other drums they were fitted with Evans heads. With such long drums, we anticipated tuning niggles, but none arose. Response was excellent and there were no overtones, just clean, powerful, spot-on toms. Quite exceptional.
MusicRadar is the number one website for music-makers of all kinds, be they guitarists, drummers, keyboard players, DJs or producers...
- GEAR: We help musicians find the best gear with top-ranking gear round-ups and high-quality, authoritative reviews by a wide team of highly experienced experts.
- TIPS: We also provide tuition, from bite-sized tips to advanced work-outs and guidance from recognised musicians and stars.
- STARS: We talk to musicians and stars about their creative processes, and the nuts and bolts of their gear and technique. We give fans an insight into the craft of music-making that no other music website can.