From design to stage, the life cycle of a Lowden
Luthier George Lowden explains the process step-by-step
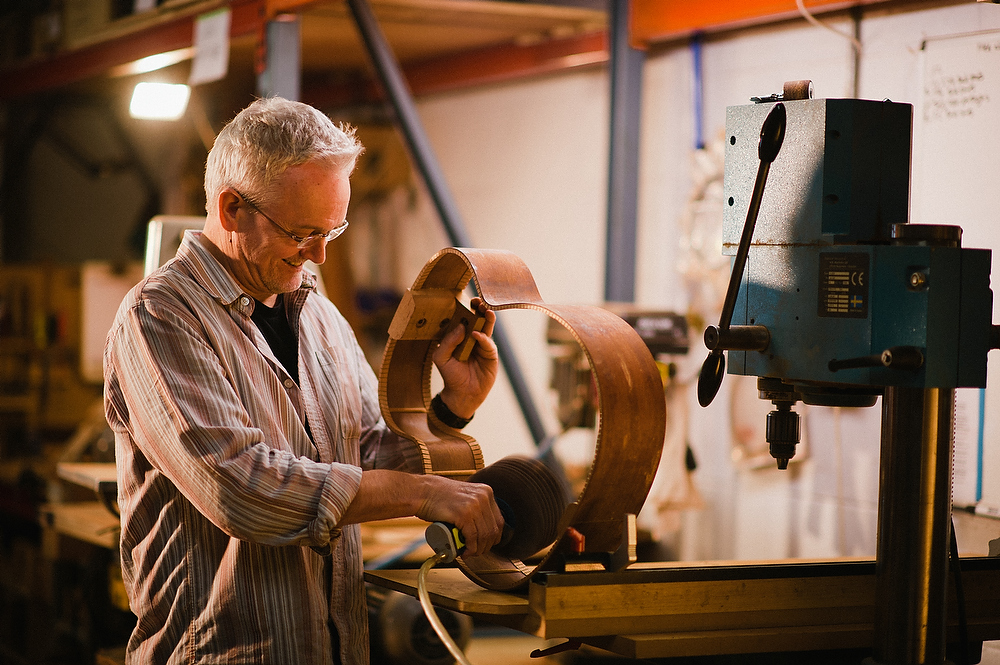
From conception to stage, the life cycle of a Lowden guitar
ACOUSTIC EXPO 2013: In this exclusive feature, we speak with Lowden founder and world-revered designer George Lowden to discover what goes in to the making of his beautiful acoustics. From initial considerations to the gleaming finished article, we document the major milestones in the creation of a Lowden guitar.
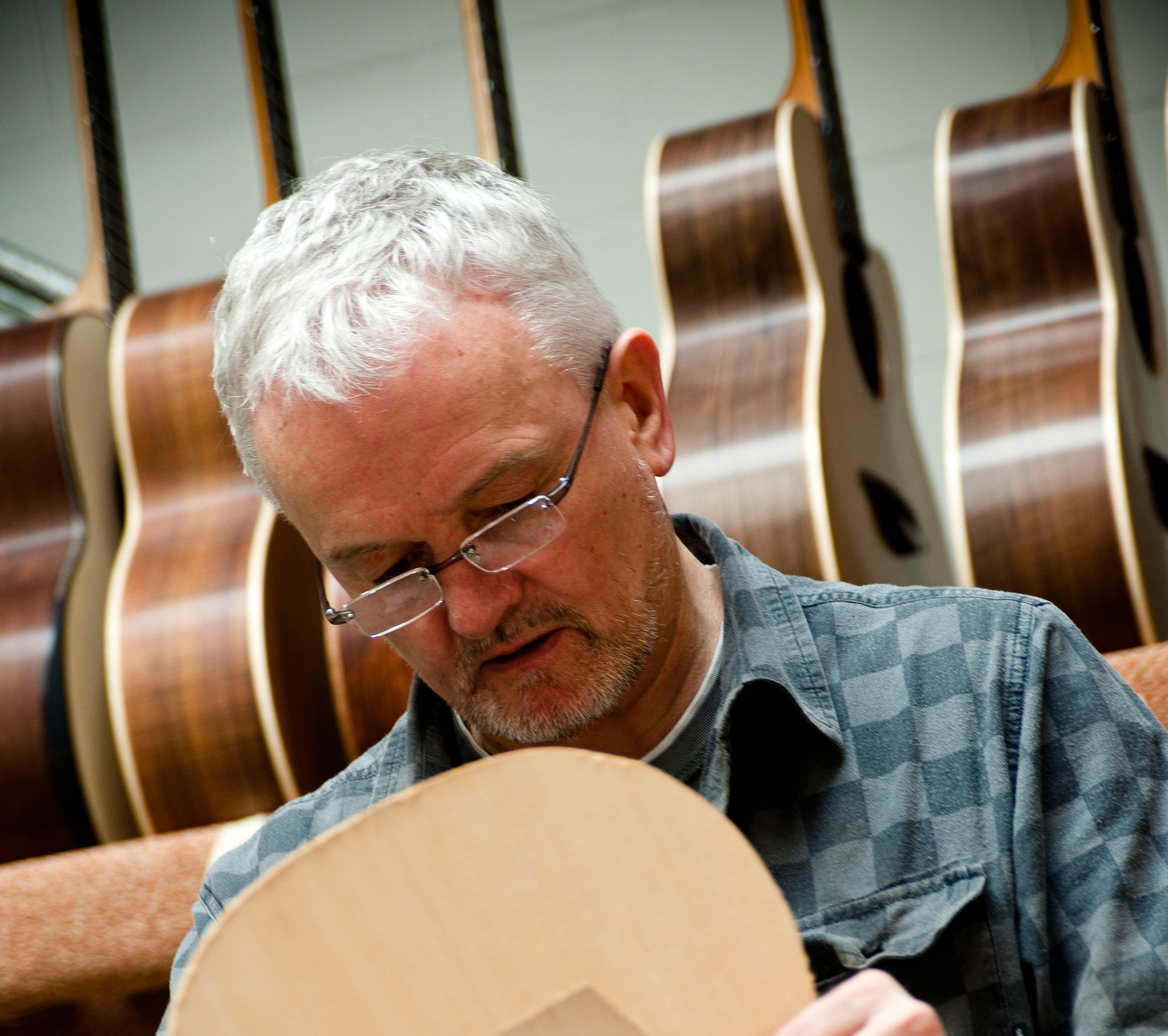
Why a Lowden?
A player decides to choose a Lowden because the guitar speaks to them. Something in its unique sound and the craftsmanship which goes into the building of it captures the heart. The Lowden guitar reflects the very personal approach and philosophy of its designer, George Lowden.
He explains it like this: "Designing and building guitars is a matter of the wood choice first, the design second, and the workmanship third. Sourcing the AAAA and Master Grade woods we use is difficult and I have built up relationships with wood suppliers who know what I want .The soundboard and soundboard strutting material both have to be split rather than sawn.
"When wood is split , the split line follows the grain direction naturally whereas when it is sawn there is no guarantee that the sawn line will be parallel to the grain. This is important because if the wood fibres are very long (as in the split line) the transfer of sound is fast and efficient, and because wood which is split is stronger than wood which does not have long parallel grain."
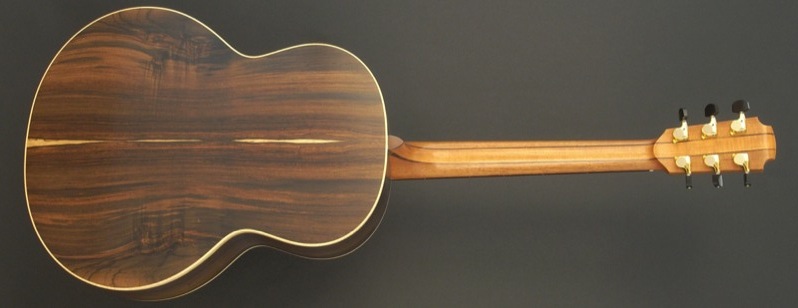
A choice of wood
"All woods give slightly different tonal responses and I will often advise players which might suit them best according to their playing style. For backs and sides I choose hard, very fine textured woods such as African Blackwood, Honduras Rosewood and American Claro or Bastogne Walnut (with Brazilian Rosewood, only very old wood is now available as new wood is not permitted to be cut down).
"I like very old Spruce, Redwood and Cedar trees (which have fallen down naturally) with a slow growth pattern for very lightweight, stiff, straight-grained soundboards. When I tap the wood I look for a certain high frequency bell-like tone. I can tell from the appearance of the wood including the prominence of the medullary rays whether the tap tone is likely to be spectacular or not."
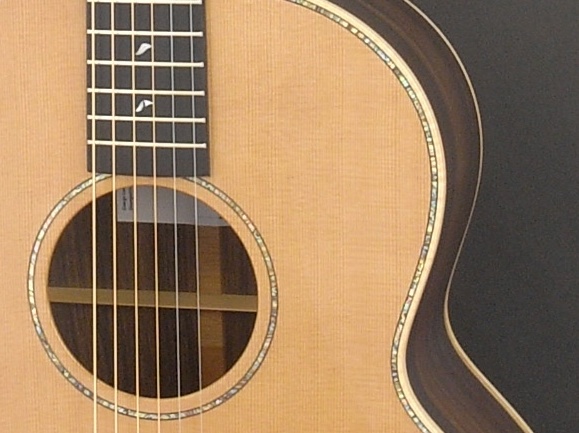
Design is also very important
"Many acoustic brands use the traditional design of older American brands. However, I have designed my own guitars and I continue to try to develop that design further. For example, building into the guitar a lot of structural integrity with a low weight / high strength ratio, and enhancing the energy produced by the strings and bridge to involve as large an area of the soundboard as possible. The aim is to ensure that all the individual elements of the design work together to create a truly responsive guitar – capable of great subtlety on the one hand, yet very powerful on the other."

Skilled craftsmanship is key
"Workmanship is equally important for long term integrity and to eliminate unplanned-for stresses within the guitar. If you just ensure structural integrity but neglect to ensure that all joints are an easy natural fit, then the guitar will sound tight and not responsive enough. We use Japanese hand tools with razor sharp cutting edges, employing a depth of concentration which permits very fast work to an extremely high standard at the same time.
"Today’s guitar makers benefit from several hundred years of stringed instrument building tradition and I value that very much. But I also hope to add my ideas to this tradition in some way, to perhaps benefit guitar makers in the future. I endeavour to make my guitars very responsive and do not compromise on workmanship or attention to detail in the design. The guitars have to be easy to play, and most of all, they have to inspire the musicians to create new music!"
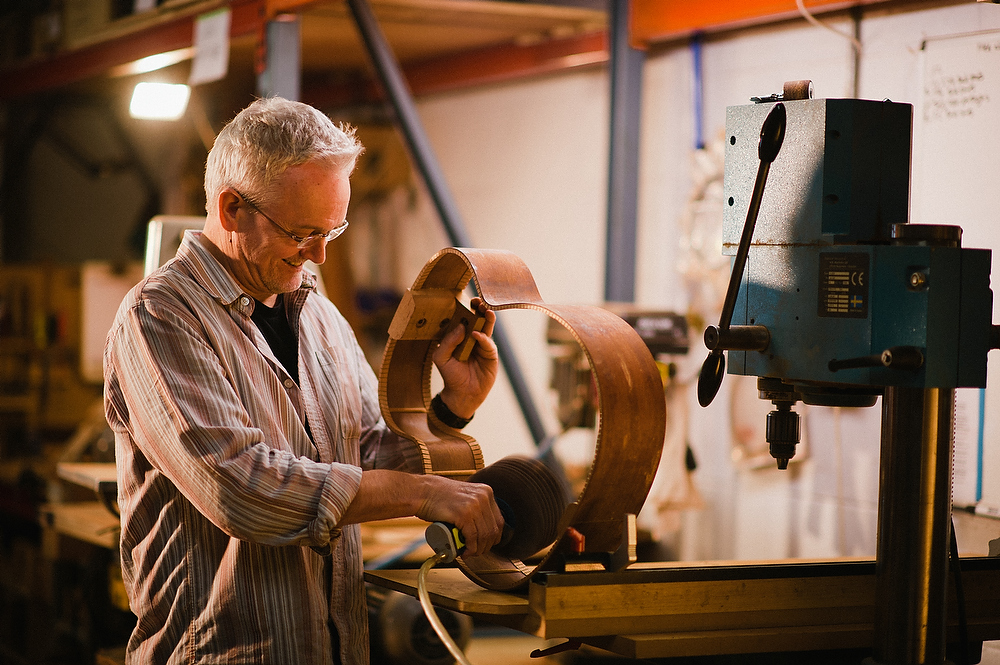
The making process begins when...
"Bookmatched sets of backs are paired with sets of sides which have the same colouring and grain. The sides are bent using special presses then finished by hand on a bending iron. They are hand jointed, ensuring the join is perfect. The soundboard is jointed in a similar fashion and the soundhole is cut out and inlaid. The bracing struts are fitted and carved by hand in a way that maintains the stiffness of the soundboard at key points whilst reducing the weight, thus accentuating the tonal characteristics of the chosen body shape (O, F or S). The back, sides and top are glued together and left for 24 hours for the glue to fully cure."
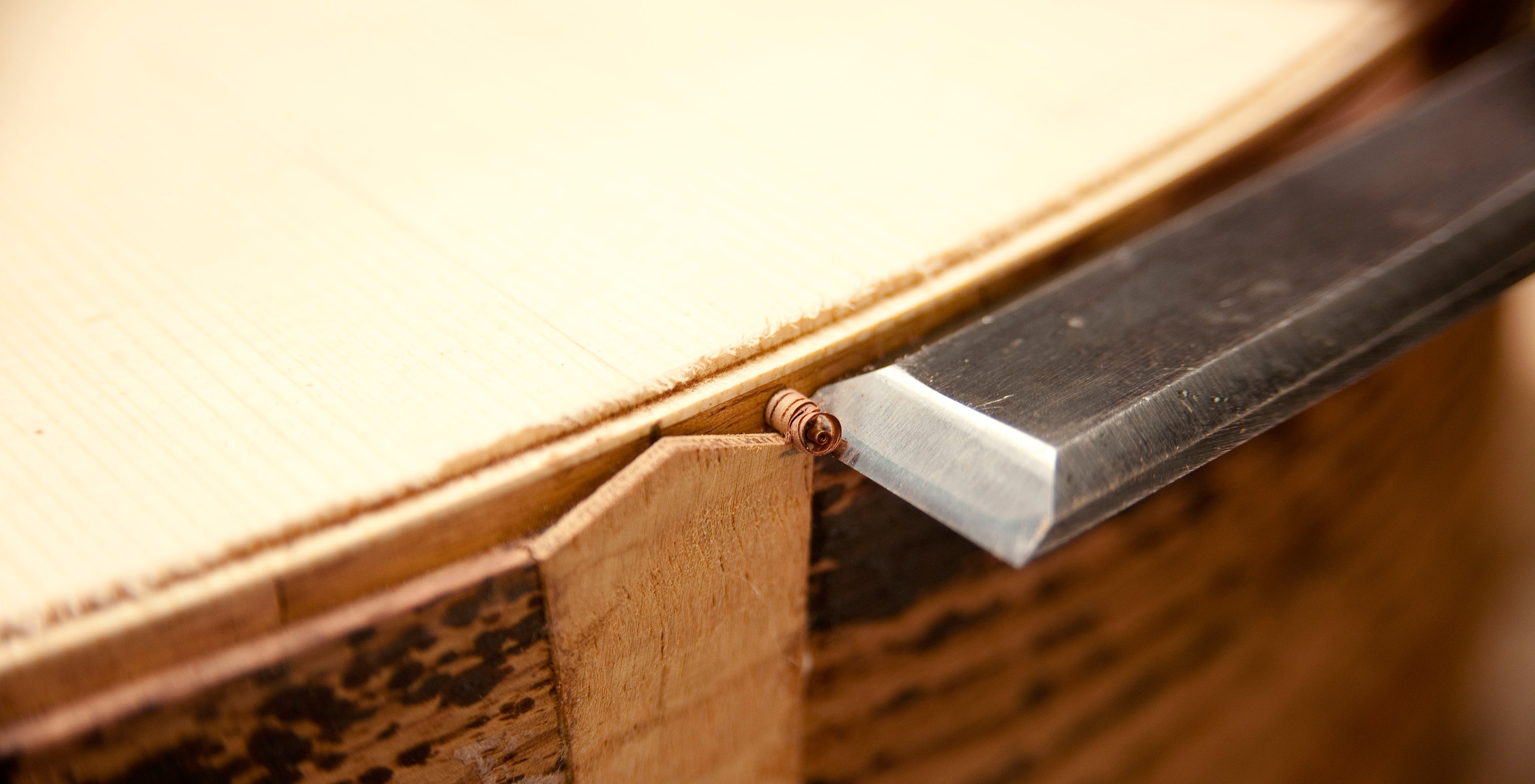
The soundbox is now ready to be inlaid
"Channels are hand-routed around the outside of the guitar and the exotic wood bindings are hand-bent then glued into the channels. A special inlay for the strap button is fitted at the bottom of the guitar. The bindings must be mitre-jointed to this inlay by hand, matching the angle of the strap button inlay exactly. The inlays are then scraped by hand to remove any glue."
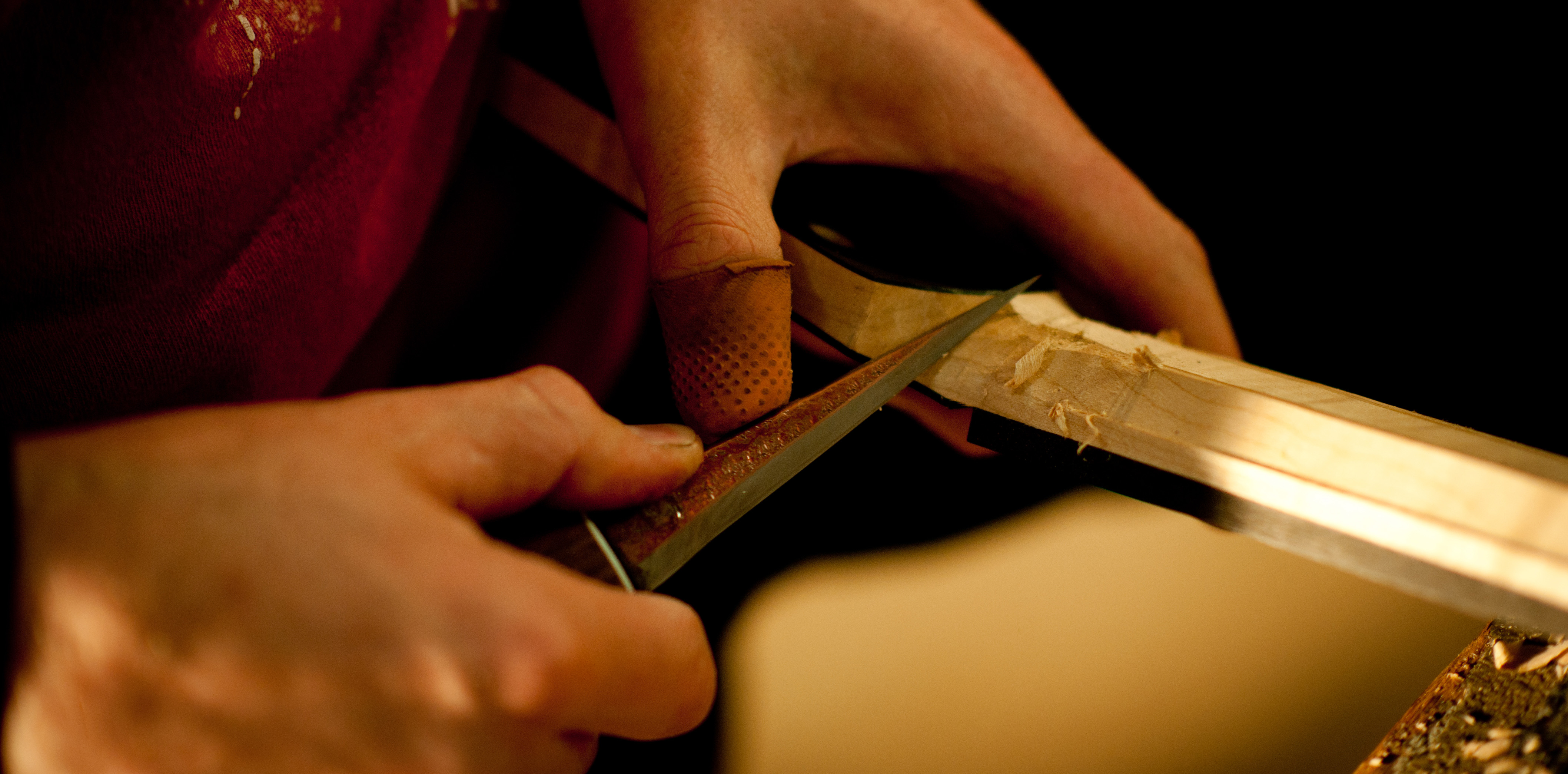
All Lowden guitar necks are carved and fitted by hand
"This is done using a spoke shave and a hand-made Japanese wood carving knife. There are different profiles and widths to suit a variety of playing styles. It is then fitted to the guitar using a dovetail joint which is adjusted by hand, ensuring the neck is perfectly straight with a tolerance of around 0.2mm"
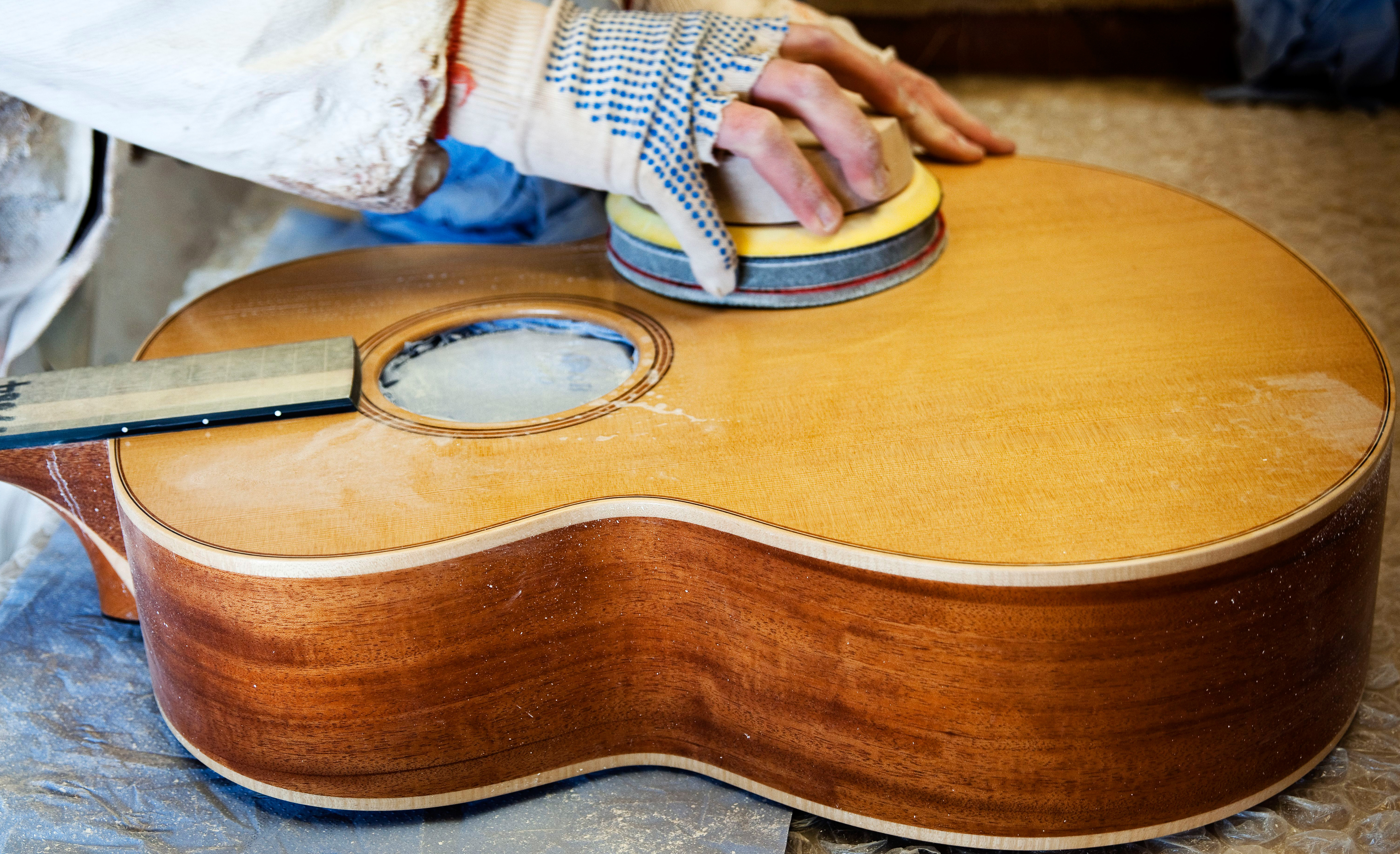
The polishing process takes around a week
"The whole guitar is sanded, removing any dirt or glue from the wood, then sprayed by hand. Each guitar receives three coats of polyurethane lacquer which is hand-rubbed to a satin finish of around 150 microns – or half as thick as a piece of paper – to ensure the wood’s natural vibrations are not restricted by lacquer."
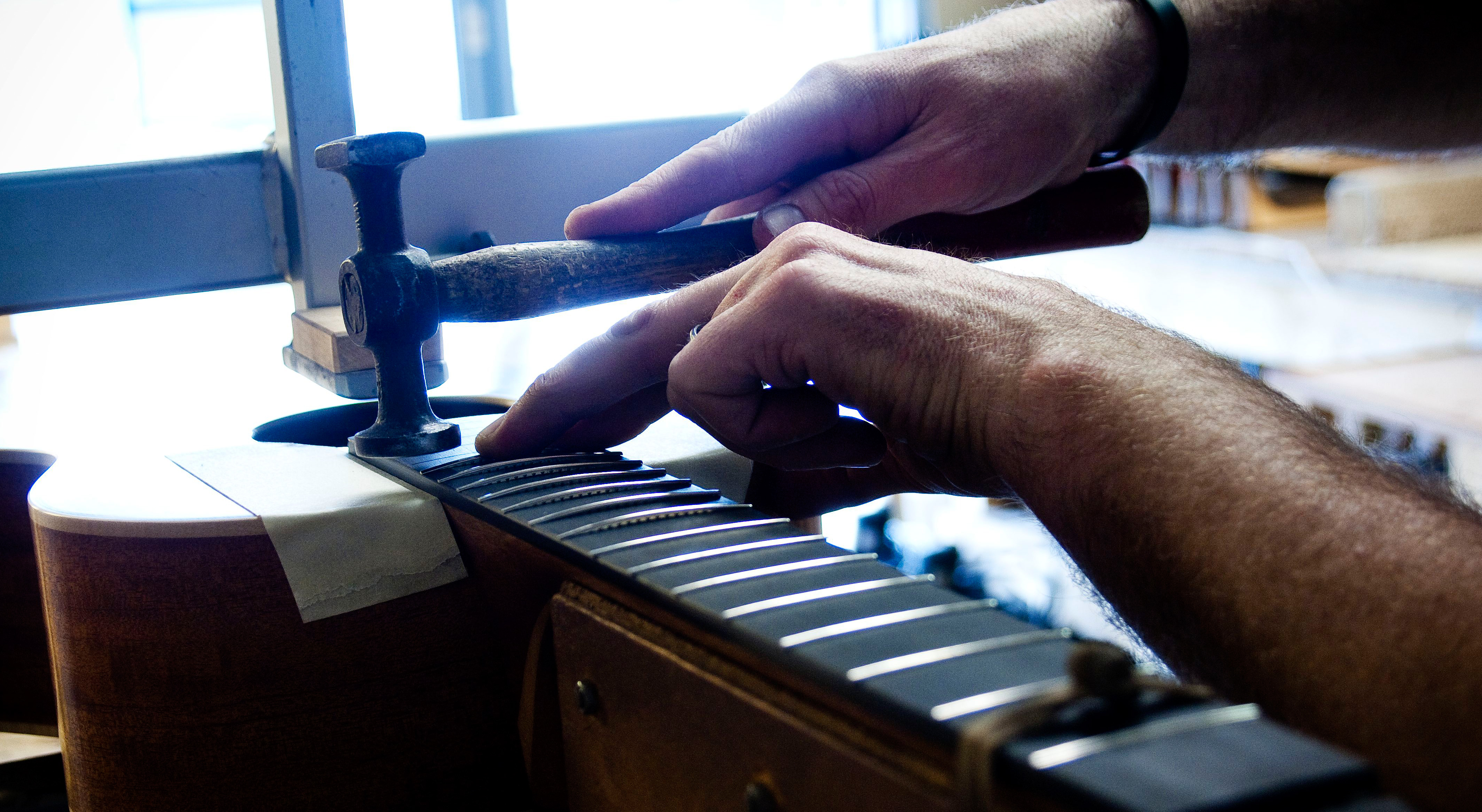
The guitar is then fretted
"The accuracy of this process is vital for the playability and proper intonation of the guitar as intonation will be adversely affected if the frets are not perfectly level. They are ‘stoned' to make sure they are level, then dressed and polished to remove rough edges."
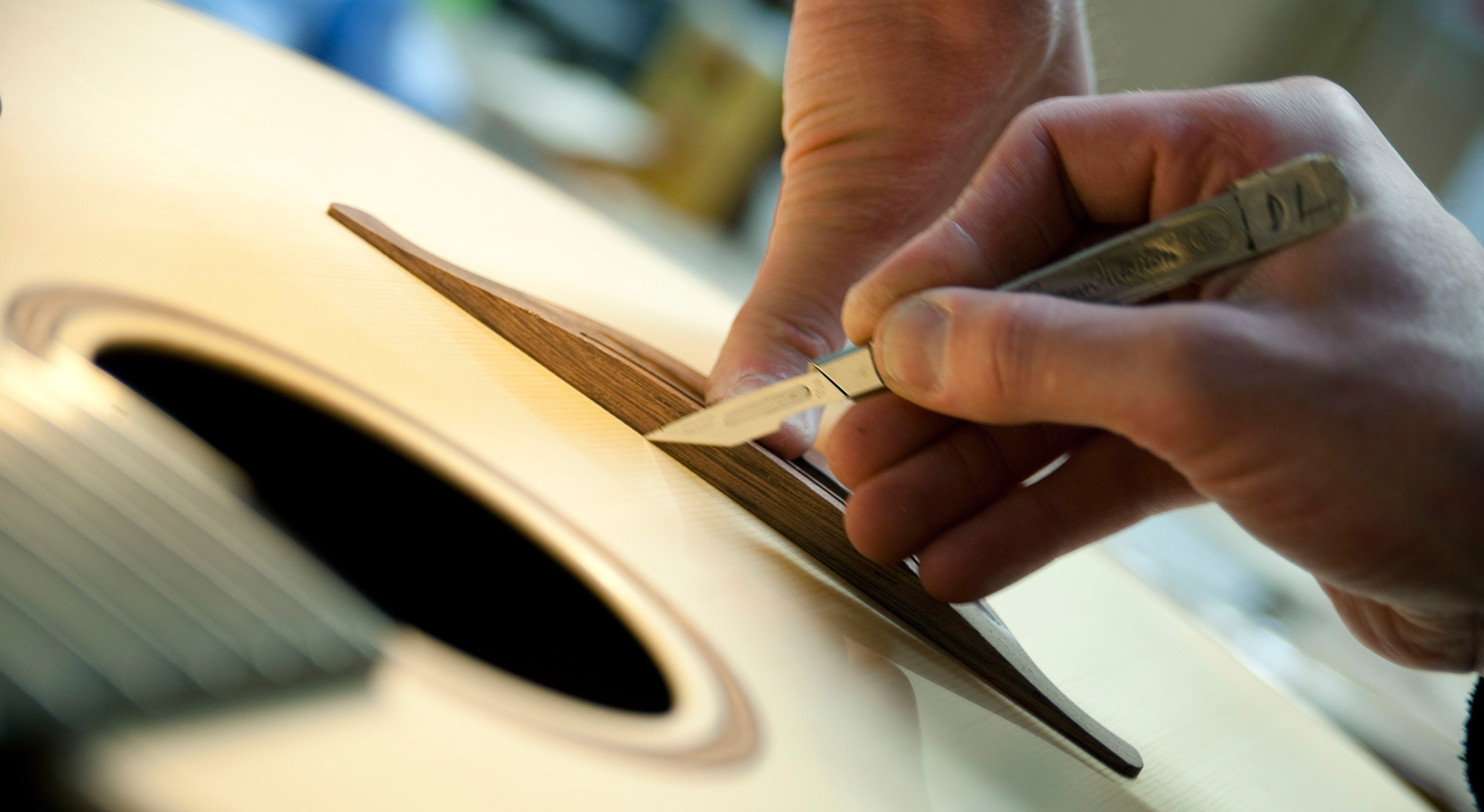
The final stage
"The final stage is where the bridge, machine heads, saddles, top nut and strings (and optional pick-up) are fitted. The machine heads are fitted first, then the cow bone top nut is shaped and the strings slots filed by hand. The bridge is initially positioned by eye and then several measurements are made to position it accurately. The craftsman holds it in position and marks its outline into the lacquer using a scalpel. He then removes the lacquer inside the scalpel outline with a Japanese chisel so that when the bridge is glued to the soundboard, there is a wood to wood contact. The cow bone saddles are then shaped by hand to ensure consistency of action heights across all Lowdens. The guitar is then set up ready for playing."
Finally, bringing the Lowden sound and beauty to life is critically acclaimed French-Algerian guitarist Pierre Bensusan with his haunting Night Song:
For more information on Lowden and their guitars, please visit their Acoustic Expo 2013 booth.