MusicRadar Verdict
There is a reason why Alan Gilby is one of the most respected UK drum makers, and these drums are a prime example of his work, offering an intriguing combination of the tonality of wood and brightness of metal. Hearing them we can appreciate why so many drummers have requested that Alan resurrect the Power-lined series, it's just a shame that a couple of cosmetic details have compromised the rating of the drums.
Pros
- +
Loud and penetrating voice. Intriguing wood and metal shell combination.
Cons
- -
Some cheap cosmetic features.
MusicRadar's got your back
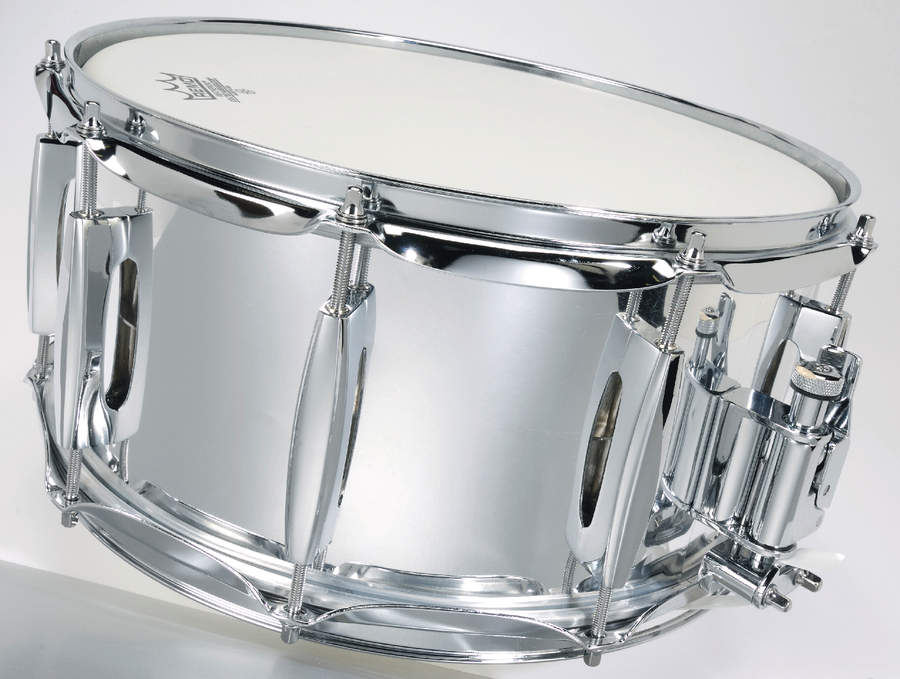
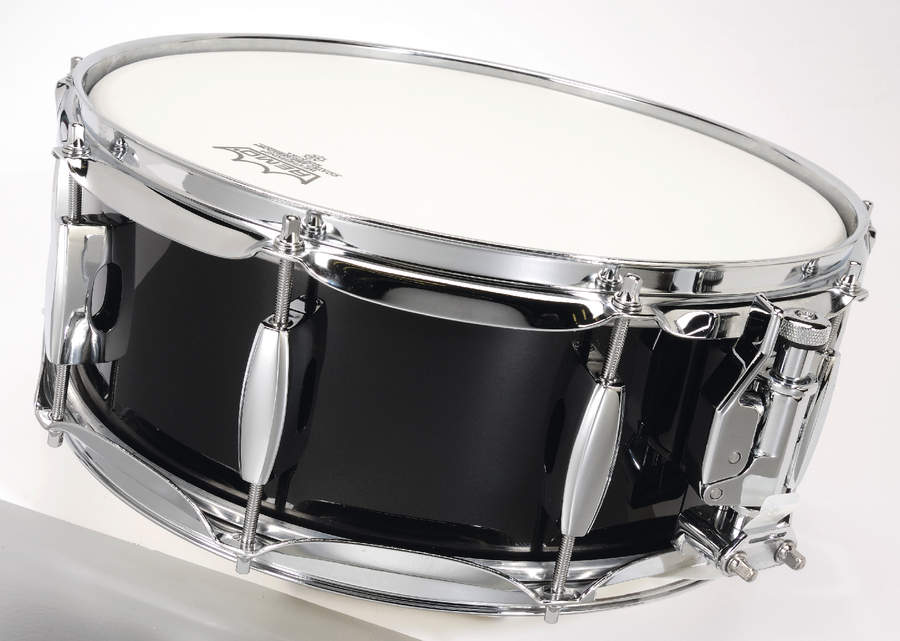
Alan Gilby is something of a veteran among British drum makers, having spent the past 33 years designing and making Richmo drums for a diverse range of customers, from classical percussionist Evelyn Glennie to punk thrasher Rat Scabies. The Power-lined snare drums reviewed here feature typically inventive hybrid wood/chrome shells.
The concept is not new - Alan first introduced Power-lined shells in the late 1980s, making entire kits with this method. However, these snare drums are the first Power-lined drums that he has made since 1990. Having been asked over the years about the possible reappearance of the Power series by drummers remembering them as ‘the loudest drums that I ever played´, Alan has finally bowed to the pressure and produced the pair of snare drums seen here.
Ironically, the original Power series drums didn´t include any Power-lined woodshelled snare drums.
Build
Where all Richmo drums are usually custom built to order, these two snare drums are examples built specifically for review. As such, there are aspects of their appearance that would normally be tailored to individual choice. What would remain the same, though, is their construction.
The shells are made from Alan´s preferred wood, Finnish birch, using his standard cross-ply method. The nine plies are arranged in alternating right angles so that the grain of the inner and outer layers runs vertically. This encourages energy transfer (in other words a quicker, more cutting response).
So far, so normal, but inside the shell nestles the power lining. This is cut from a sheet of rigid chromed styrene. Around 2mm thick in total, the styrene (a plastic composite) backing accounts for 75 percent of it. The top layer of chrome faces outwards into the centre of the drum. Once cut to the right dimensions, the sheet of chromed styrene is carefully bent into the shell by Alan.
This is a tricky operation, as each sheet wants to remain flat. This quality pays off once the sheet is installed, as it pushes hard against the shell in an effort to spring flat.
The shells are drilled for hardware fittings before the styrene chrome is fitted, so the liner is drilled through the existing holes and is then secured when the lugs are attached. This is not strictly necessary and the original Power-lined drums differed at this point. Back then, Alan fitted the lugs before the lining was installed, locating the nuts in countersunk holes inside the shell. This meant that the Power lining could be left completely un-drilled for maximum sonic reflection within the shell.
However, with this design changing a lug would be extremely difficult, as once the chromed styrene is in place it is virtually impossible to prize out. Alan´s more conventional method of drilling through the Power lining means that future maintenance is possible.
The supplied lugs are bridge style (though other models are available) and a Dunnet snare release is fitted on both drums. The finishes are simple wraps. More adventurous wraps (including pearls and glitters) can be ordered, but lacquer finishes are not available.
Close inspection of both drums revealed the fitted wraps to be of the cheap and easily marked variety. Alan assured us that this was due to time constraints on his part and added that these are example rather than commissioned drums. This is understandable, but first impressions count for a lot.
Hands On
The same factors seemed to be behind the fitting of generic Taiwanese-manufactured snare wires to the drums. Alan explained that customers can order any brand of snare wire they wish, however. The two drums - 14"x5½" and 14"x7" - nonetheless performed well and displayed startlingly different personalities.
The 14"x5½" gave a supremely tight, urgent response; the merest tickle was relayed instantly and backbeats were snapped out with searing precision. And yes, it came through loud and clear. The 14"x7" drum, meanwhile, possessed a drier but hugely authoritative voice. It was disdainful of subtle stickings and only came to life when whacked. Once in its operating range, it produced a hard, penetrating, eardrumshattering bark that would have your neighbour´s house on the market in no time.
MusicRadar is the number 1 website for music makers of all kinds, be they guitarists, drummers, keyboard players, djs or producers...
GEAR: We help musicians find the best gear with top-ranking gear round-ups and high- quality, authoritative reviews by a wide team of highly experienced experts.
TIPS: We also provide tuition, from bite-sized tips to advanced work-outs and guidance from recognised musicians and stars.
STARS: We talk to musicians and stars about their creative processes, and the nuts and bolts of their gear and technique. We give fans an insight into the actual craft of music making that no other music website can.