How Leo Fender started the guitar company that changed the world
The early years that fuelled a golden era of guitar design
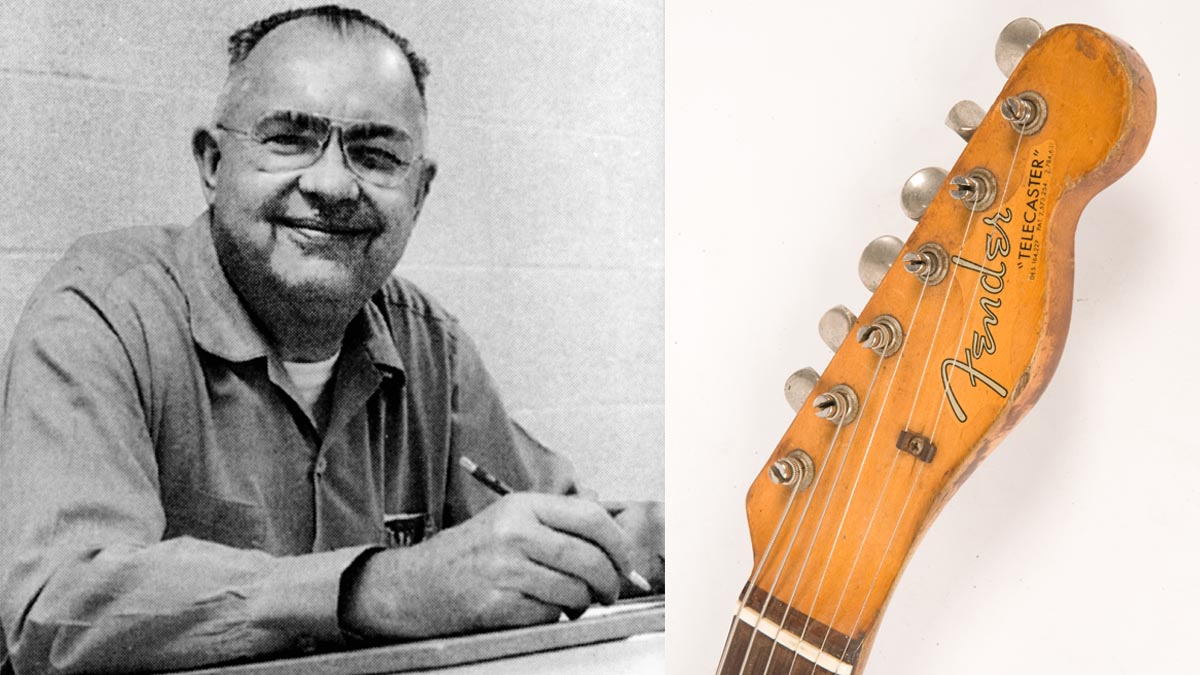
When Leo Fender and his colleagues launched the first Fender solid-body electric guitar in 1950, almost everyone who saw it thought he’d gone mad. Fender’s early amplifiers were good, but a solid-body guitar? Every player knew that guitars were hollow. They had air inside. That was obvious: they were light, and there were holes on the top to let the lovely sound out.
Every maker knew that it took craftmanship, skill and attention to build a guitar: bending the wooden sides, carving or pressing the top and back, carefully constructing a special box that transformed what guitarists played into beautiful sound.
Since the 1930s, Rickenbacker, National, Gibson, Epiphone and others had made some electric guitars. They were archtop hollowbody guitars with built-in pickups and controls, but (with honourable exceptions) they’d had little effect on players. Gibson set the style for the best hollowbody electrics and had just launched the accomplished ES-175.
The Fender Strat and Tele prototypes that reveal what might have been
Leo, however, was thinking outside the box. In fact, he decided to make a guitar with no box at all: a solid-body electric. Rickenbacker had launched a solid-ish Bakelite guitar in 1935, but it was small and awkward. Around 1940, guitarist Les Paul built himself a trio of guitars with solid through-necks. And in 1948 – about 15 miles west of Fender’s operation in Fullerton, California – Paul Bigsby built an electric with a solid through-neck for guitarist Merle Travis.
Leo Fender’s new solidbody guitar – at first called the Esquire, then the Broadcaster, and finally the Telecaster – was, in contrast to these experiments, aiming for commercial success.
Lone vision, team effort
Leo took a few piano lessons before trying the saxophone (never seriously), and never learned the guitar
Leo had started his working life in the 1930s as an accountant. He’d been unfit for military service in World War II – losing an eye after a childhood illness – and during the war continued to run his radio store.
When the war finished, he ran a short-lived company, K&F, making lap-steel electric guitars and amps with his friend, guitarist Doc Kauffman. But by 1946, he had a new operation called Fender Manufacturing. Leo continued to make the steels and amps, now with his new Fender logo, and expanded into new premises in Fullerton.
Want all the hottest music and gear news, reviews, deals, features and more, direct to your inbox? Sign up here.
Doc had left the partnership because he was fed up with Leo’s single-minded, workaholic ways. Leo was an introverted, hard-working man, prone to long hours and happiest when by himself, drawing up designs for another project or playing with a new machine. As far as he was concerned, the fewer people who got in the way of all this, the better.
And generally speaking, Leo was – according to Leo – the only one able to get such things done. Yet he wasn’t even a player; Leo took a few piano lessons before trying the saxophone (never seriously), and never learned the guitar.
But he thought if there was a product on the market, he could build it better and cheaper – and make a profit in the process. Despite spectacular later successes, during the early years the new Fender company came perilously close to failing. It was Leo’s sheer determination and his luck in surrounding himself with clever, dedicated people that would help it to overcome the problems in these difficult times.
Don Randall became a partner with Leo in the Fender company, heading up the sales arm of the business and becoming arguably the most important person in the development of Fender’s success. George Fullerton joined Fender in 1948 and soon became what one colleague described as “Leo’s faithful workhorse”.
Leo’s wife was important, too. Lack of cash flow was almost ever-present at Fender in the early days. There were times when it was hard to cash Fender cheques – especially if Esther Fender was late in receiving her wages from the phone company where she worked.
Bob Perine of the Perine-Jacoby agency took over Fender’s advertising in 1957, starting the classic, ‘You won’t part with yours either…’ series of ads. Forrest White joined the team in 1954 to take over the running of the Fender factory. He reorganised this vital part of the business into an efficient and effective production base.
Music for the masses
Fender’s team was now in place and their mass-production techniques at the Fullerton factory worked a treat. There were all kinds of machines, some for winding pickups – Heath Robinson affairs with wheels and pulleys – while one area housed a few ad-hoc finish spray booths alongside a wall of racks for drying sprayed bodies.
There were punch presses for making metal parts and benches for final assembly. A worker would screw on pickguards and bridges and tuners, and then another would take over and solder the electronics together. Finally, new guitars would be strung up and tested through a Fender amp that was lifted from the line.
Most Fenders of the early 1950s came only in standard finish: blonde for Teles, Esquires and Precisions, sunburst for Strats. But by 1956, ‘player’s choice’ coloured guitars became an option, and during the following year these DuPont paint finishes were appearing in Fender’s catalogues as ‘custom’ colours, a label that has stuck ever since. Players began to see Fenders in Dakota Red, Lake Placid Blue, Inca Silver, Surf Green and the rest, but generally declined to hang such gaudy things around their necks. This means they now fetch small fortunes.
Fender entered the 1960s in buoyant form. In July 1962 the price-list included nine electrics (these were the Duo-Sonic, Esquire, Esquire Custom, Jaguar, Jazzmaster, Musicmaster, Stratocaster, Telecaster and Telecaster Custom) and three basses (Precision Bass, Jazz Bass, and VI), with 13 amps, five steel guitars and two pedal-steels completing the line-up. But come 1965, a surprise was lurking. Leo Fender would sell the company [to CBS] that still bears his name.