The workshop: Manson Guitar Works
The British maker that can boast of builds for Matt Bellamy, John Paul Jones and Dave Grohl
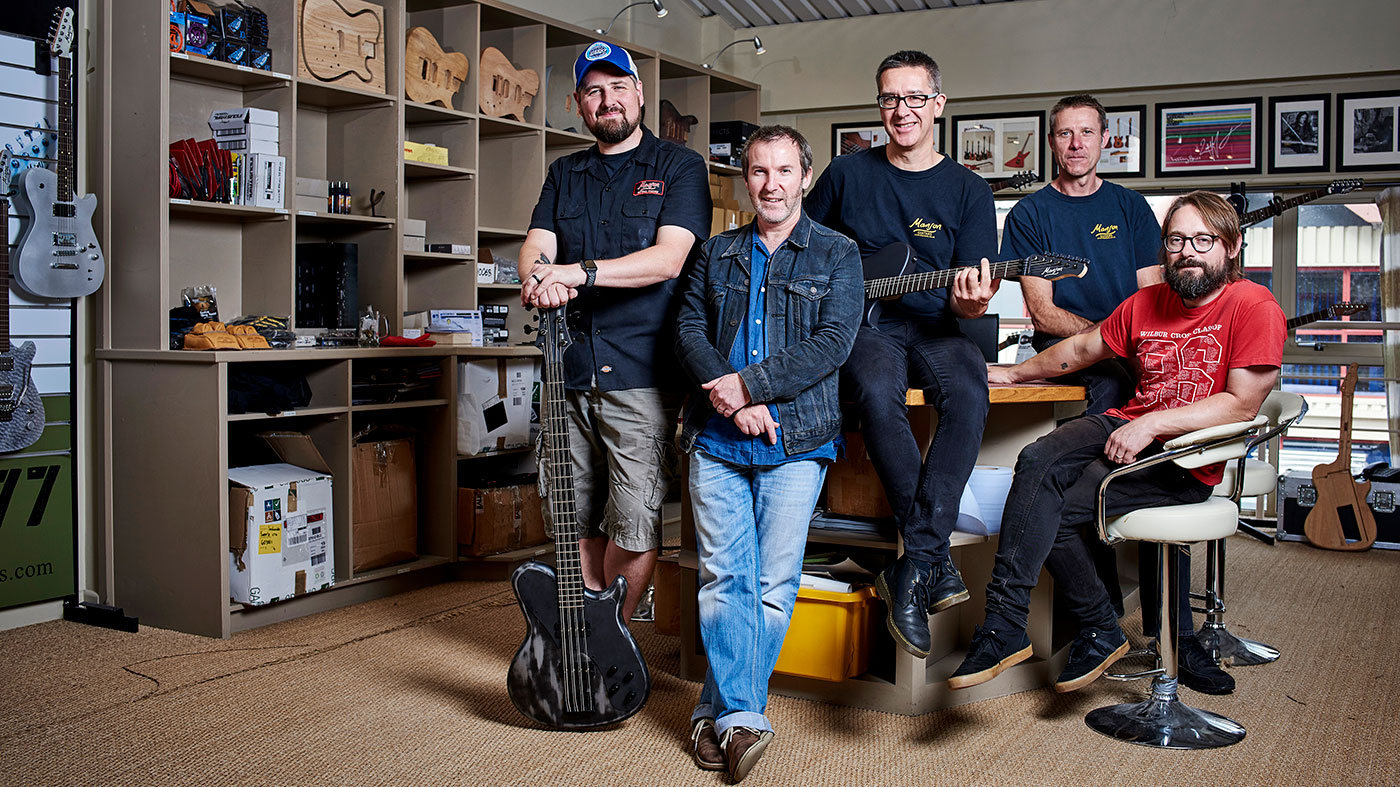
Luthier Hugh Manson has been realising the dream designs of musicians for many years. The triple-neck acoustic and signature bass for Led Zeppelin legend John Paul Jones, the MIDI guitars for Muse’s Matt Bellamy, and the ‘Swiss Cheese’ metal guitar you might have seen in the hands of Foo Fighters’ Dave Grohl have all emanated from Hugh’s Devon-based facility.
Many Devonians will be familiar with Manson’s retail outlet in Exeter, but today our journey takes us a little further southwest to the workshop at Ashburton, a positive hive of industry, where customers’ drawing-board dreams are turned into wood-and-wire reality. Our guide is Manson Guitar Works CEO, Adrian Ashton.
Customers can come to the premises here by appointment and we can sit down with them and talk about design details, woods used, pickups and electronics
“Originally, I was a customer of Hugh’s and ordered some custom basses from him, which I absolutely fell in love with,” he tells us. “That led to the opening of the shop in 1992 where I was heading up mostly the retail side of things and Hugh obviously was being the luthier that he was. Over time, as the shop grew, expanded and became more successful and more known around the world, the luthier side obviously started taking a bit of a backseat.”
Around eight years ago, the company took a long hard look at the artists they had been building for and supercharged the operation in order to make a return to the manufacturing side of the business. Originally sited at the old Manson premises in Exeter’s Rackclose Lane, the rapidly expanding company soon made the move to its current location where the Manson range is now managed, including the custom builds.
“Customers can come to the premises here by appointment and we can sit down with them and talk about design details, woods used, pickups and electronics,” Adrian explains. “That’s the higher end of the guitars, prices from £2,500 and upwards.”
Manson’s MA and E series have the woodwork done in Europe, demand for these models being such that the company’s original premises wouldn’t have been able to keep up with the numbers involved. But a change is in the offing here, as the intention is to do much more of the building in the new expanded premises.
“Then customers can order those guitars but can spec all kinds of different changes from colours to electronics, to custom circuits to MIDI controllers,” Adrian affirms. “Those prices are from £1,000 to £3,000, so it fits a really nice price point for the customer.”
Want all the hottest music and gear news, reviews, deals, features and more, direct to your inbox? Sign up here.
Then there is the arrangement Manson has with Cort: “They manufacture Hugh Manson’s designs under licence, which has produced the Matthew Bellamy MBC-1, the new M-Jet and the classic TC.”
There are modifications on offer here, too. “We also find, because of our reputation for customising and modifying, that many of those come back to us for modifications and upgrades to try and give more of a boutique and unique feel, but we’re looking now at the £400 to £600 price point.”
Origins of signatures
As we’ve seen, Muse’s Matt Bellamy is just one of Manson’s celebrity customers and one that has a whole battalion of Hugh’s instruments at his disposal. We wondered how many guitars the company has built for him.
“Lots,” laughs Adrian. “Hugh and Tim [Stark] have worked extensively with Matt, and Tim was involved in the crazy doubleneck guitar, which was one fretless neck and one fretted. That was incredible. Obviously, the MIDI screen controller guitars, there are lots of variations of that, the Bomber guitar with the LEDs coming from it, the Drone guitar with the military theme… I mean, it’s a real honour to be making signature guitars for John Paul Jones from Led Zeppelin and Matt and all the other artists we have.
These are the only signature guitars these guys have used and they’re basically some of the biggest names in the industry
“These are the only signature guitars these guys have used and they’re basically some of the biggest names in the industry. We’re not a very small company and we’re not a very big company, so it’s an amazing experience to be involved in the design process and working with these people. What a great job; you come to work and you have to remind yourself sometimes of the things we do here!”
What sort of demands are made for custom finishes and things like that? “Lots of crazy finishes: mirrors, cracked mirrors, metal paint guitars, aluminium guitars, the original DeLorean. In terms of numbers of different designs, there are a lot. Then actual numbers of guitars that Matt uses for touring or has taken out with him… Gosh, it must be close to the fifties, hundreds.”
Bringing it back to a more standard customer level, where does the design process start for them?
“What we find most customers want to order is one of our already established shapes. We have a good range,” says Adrian. “There is the E-Series through-neck that appeals more to the rock guys with the extended horns, six and seven-string versions. We’re already set up to do any kind of custom version of that particular shape and body style. Then there is the MA shape, which, of course, we’ve seen recently on the Mikey Demus. Basically, the body outline is the MA shape, even though it’s a very different-looking guitar to what we call our MA EVO.
“We find probably 80 per cent of our custom work is people designing their preferred spec on a layout such as that,” says Adrian. “But we also do full custom. Tim has done some double-neck basses recently for customers. We did one for Nick Beggs, who is often on tour with Steve Hackett and so obviously a double-neck was a requirement in the Genesis Revisited tour. There is such an extensive catalogue of Manson guitars and different designs – we can show people work that’s been done in the past by Hugh and Tim. They might get an idea from that.”
What about if someone approaches you with a completely new idea? “If it’s going to be a completely new design to the customer specification, we’ll do a set of drawings. Then we’re usually going to template up to make sure there is accuracy, even though it’s a one-off guitar. That will be the starting point to show them the visuals so they can go, ‘Yes, that looks great.’ Then we’ve been spec’ing guitars for decades, so we can usually help the customer if they tell us the sounds and playability they’re looking for, how important weight is. We can guide them with things like woods, technology, pickups, hardware towards the end result.”
Future proofing
During our tour of the Manson workshop, our discussion turns to the current trends in bodywoods, especially in view of CITES regulations making certain tonewoods difficult to import. What are people going for at present?
“Swamp ash is very popular because of the lightweight element,” says Adrian. “You get great tones from swamp ash. Of course, it would only form part of it, but it does seem to be very popular, whereas seven or eight years ago it seemed to me that mahogany was the popular wood. I think so long as there is choice and so long as the customer has an idea of what they want sound-wise and what they want weightwise, we can usually direct them to a couple of tonewoods that will satisfy them.”
Yes, we have that technology, but if you took that off it is still a great, great rock, blues, folk, jazz, metal guitar underneath
And have the CITES regulations had much of an effect on the business? “I think we’re going to see quite a bit of change on that in the next five to 10 years to come. But we’re at a nice size where we can make quite rapid changes so we can accommodate that. We also have some good stocks of wood to keep going for the next few years. It’s probably not the time and place to go into CITES and international law, but I mean, just personally, I find it interesting that what sparked the CITES implementation was furniture being made from solid rosewood and being illegally harvested and imported.
“It seems to me that that’s probably the thing that needed to be stopped rather than stopping guitar makers, mainly who have very good green credentials and usually are thinking about the best way to maintain longevity of wood stocks. But you can’t argue with the result. We have reduced our rosewood consumption to almost nil because of the licensing required to export it. But rather than view it as a problem, [we] view it as a challenge to see what alternative woods there are. It’s been good for that.”
Despite the fact that Manson guitars are shipped all over the world, the team in Ashburton is relatively small and intent on keeping the quality of its instruments as high as possible with innovation at the heart of the business.
“We’re doing a lot of things with guitars that no-one else has ventured or done before,” Adrian agrees. “Things like the MIDI controllers – and this technology is sometimes seen as the main thing on the guitar. I mean, you see that great big MIDI screen we put on the front of a guitar; it’s going to grab everyone’s attention. But I always say to people, ‘Yes, we have that technology, but if you took that off it is still a great, great rock, blues, folk, jazz, metal guitar underneath.’ We make a great guitar first, then think about the crazy finishes.”