The complete history of Yamaha Drums
The inside word on the return of the Recording Custom
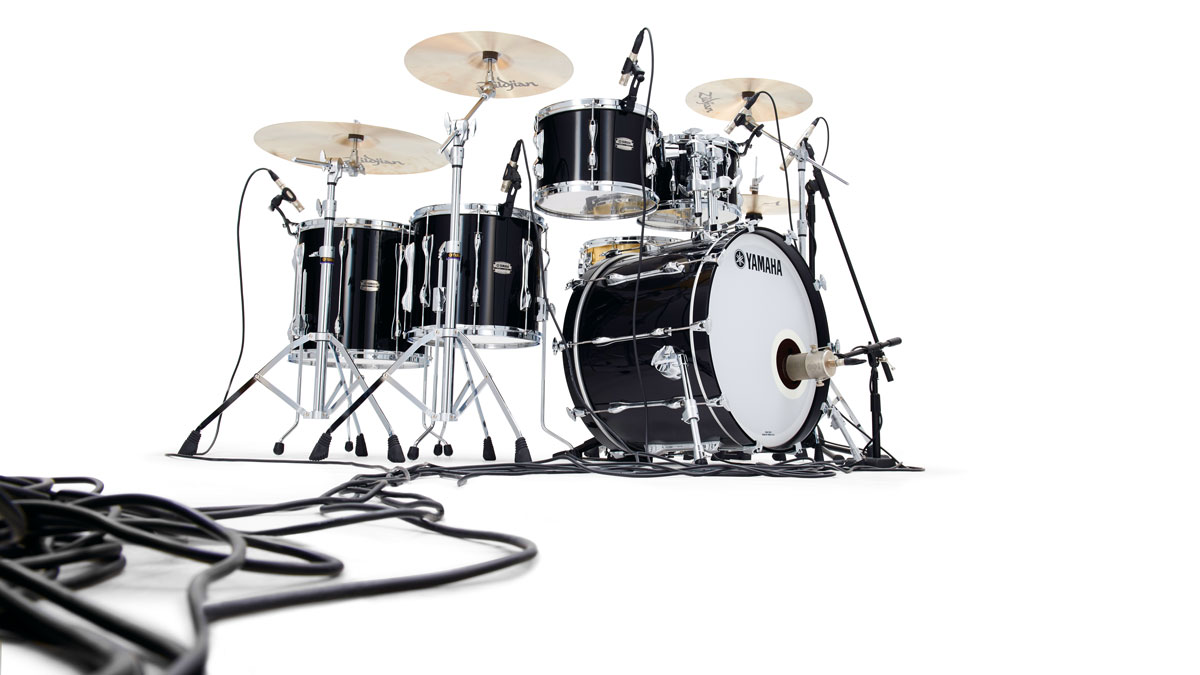
The history of a drum legend
Although Yamaha was founded way back in 1887, it has only been making drums since 1967. From the off the drums were of high quality, hand-crafted in a relatively small workshop in Hamamatsu.
Up till 2011, all of Yamaha’s high-end drums were made in Japan. And although Yamaha continues to build its flagship Phoenix PHX series in Japan, the latest professional series are now coming out of the new facility in Xiaoshan, China.
This extensive plant was first opened in 1997, producing Yamaha’s woodwind and brass instruments and marching percussion. Then in 2010 Yamaha achieved a long-held ambition to add a dedicated drum building, employing the latest in hi-tech, environmentally strict and rigorously quality controlled production methods. The aim as always is to stay on top, be competitive and to build the best drumsets conceivable.
The new Recording Custom has badges which clearly state ‘Made in China’.
Xiaoshan first delivered the Live Custom series, followed by 2014’s truly progressive Absolute Hybrid Maple. Now we have the revamped Recording Custom series, launched at Winter Namm, 2016. The
Recording Custom is Yamaha’s most acclaimed kit, quite possibly the most recorded kit ever, the kit which put Yamaha out front throughout the 1980s.
The new Recording Custom has badges which clearly state ‘Made in China’. Yamaha’s Xiaoshan facility is not some tawdry operation to make drums on the cheap using casual labour. On the contrary, Yamaha has invested an unheard-of US $10 million in the operation, with the Chinese workforce trained to the highest skill levels by the ultra-experienced Japanese craftsmen.
Visiting the factory was eye-opening, seeing up close the exacting manufacturing tolerances and testing, the unstinting quality control, the laboratory-style cleanliness of the workplace. That the factory is in China is simply a sign of the times we live in.
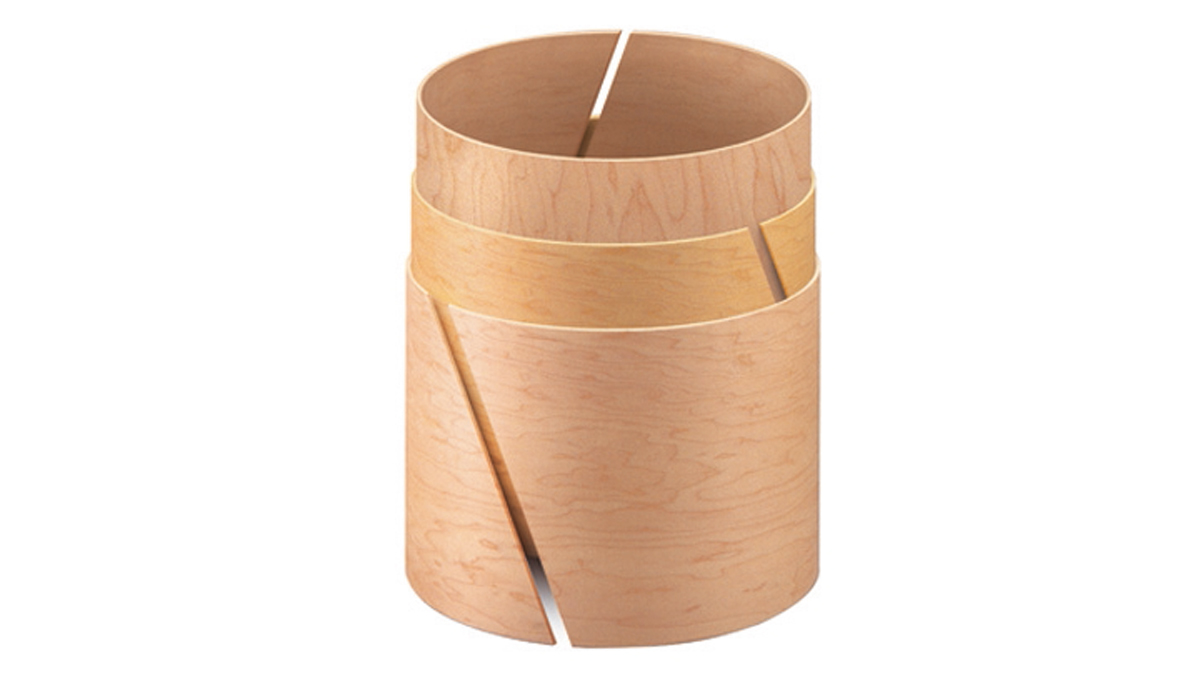
One man's Vision
Yamaha was originally founded as a musical instrument company by a Japanese watchmaker called Torakusa Yamaha, who lived from 1851 to 1916.
He was one day asked to repair a portable reed organ, and with his fascination aroused, he set about building his own instrument. This was in 1887, the date of his company’s birth. Gradually he saw the potential for producing Western musical instruments in Japan.
Two years later he set up the Yamaha organ manufacturing company in Hamamatsu, which became the Nippon Gakki Co Ltd in 1897. By the turn of the century Yamaha had its first upright piano and a couple of years later in 1902 its first grand piano, which already looked very much like the pianos of today. Keyboard instruments have remained a lynchpin of the company ever since, and today Yamaha pianos grace concert halls, jazz clubs, studios and homes all around the world.
First drum kits
In the mid-1960s, with the youth and music revolution that was energising the world, Yamaha honed in on recreation and lifestyle markets, starting with wind instruments in 1965 and establishing the Yamaha Music Foundation the following year. This expanded into Europe with Yamaha Europe GMBH in West Germany. Yamaha was a well-known and respected brand well before setting to work on drums in 1967.
The first kits were manufactured in Hamamatsu, Japan. Just as today we may be sceptical about the ‘Made in China’ tag, back in the 1960s ‘Made in Japan’ was not greatly assuring. Hard to imagine now, but in any case this perception was to change quickly and dramatically.
Just as today we may be sceptical about the ‘Made in China’ tag, back in the 1960s ‘Made in Japan’ was not greatly assuring.
Right from these earliest efforts Yamaha devised its distinctive shell-making procedure which is universally regarded. This is the famous air seal system with staggered diagonal seams. The air seal method involves placing the wood plies in a circular mould and then inserting an air bag under great pressure, thus imparting a perfectly even force all around the inside of the shell, creating a more exactly circular shape.
Added to this, cutting diagonal joins for the staggered plies means that as plies are slotted into the shell they can be pushed down until the seams are absolutely tight, thus avoiding the gaps which easily occur in conventional (vertical) straight seams where the measurements do not quite meet up.
Yamaha continued developing its lines to include the pro YD7000, budget YD5000 and starter YD3000 series, which were all PVC wrapped.
In Japan this method was traditionally known as kachikomi, and creates such a strong structure that even with thin shells there is no need for reinforcing rings. With vertical seam construction you sometimes see tiny air gaps left inside the shell, or slicks of filler applied to the inner ply to close the gap. With diagonal seams this small but unsightly inaccuracy is eliminated.
Yamaha continued developing its lines to include the pro YD7000, budget YD5000 and starter YD3000 series, which were all PVC wrapped.
Then in 1975 came the first incarnation of the YD9000, Yamaha’s all-out assault on the top-end drum market. What distinguished the 9000 was the 100 percent birch shells, the full-length high-tension cast lugs and the Yamaha System hardware, which was also unveiled in 1975. Taken all together this proved a mighty threesome.
The birch required for drum building was a broad-leafed indigenous Hokkaido variety that had previously been used by Yamaha in its piano production. Bass drums were eight-ply while toms were six-ply and bearing edges were cut at 60°. At this stage finishes were wrapped or natural wood. The original full-length lugs also had internal springs.
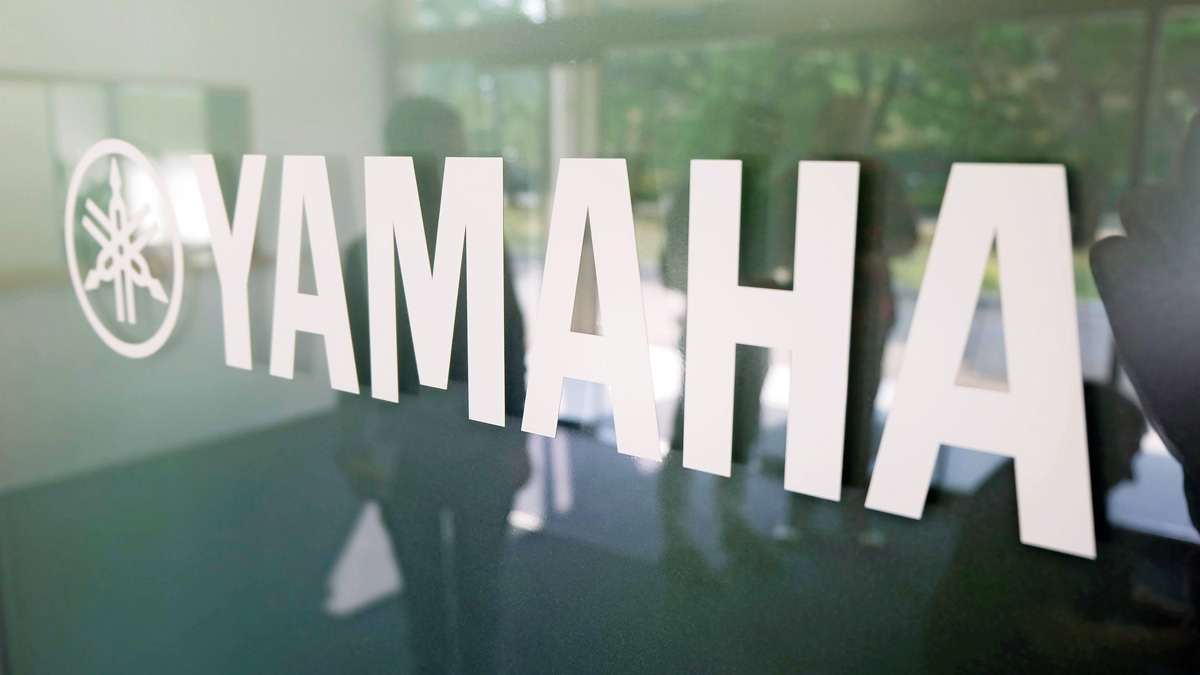
System Drums Hardware
In 1977 Yamaha expanded into overseas drum production, opening a facility in Taiwan.
A different version of the 9000 was built called the YD9000D and it lacked the full-length braced lugs. Yamaha’s tight budget at the time could not stretch to investing in moulds for the Taiwan factory.
Instead it had the earlier ‘YD’ shaped single lug, minus the internal spring. Despite rather missing the point, it must be said this was a good looking kit and has a scarcity value today.
Steve Gadd was involved in the design details and his Black Piano Lacquered kit would become the most desired and copied in the drum world during the 1980s.
The Taiwan operation lasted for three years after which the extra production load was taken on by Sakae back in Japan.
Meanwhile, in 1978, the series had moved onto the Japanese-crafted YD9000R. This was when Yamaha’s experience and expertise with piano lacquering/painting techniques were adapted to the drums, causing a genuine sensation in the drum world. Steve Gadd was involved in the design details and his Black Piano Lacquered kit would become the most desired and copied in the drum world during the 1980s.
Recording Custom at last
In 1982 Yamaha invested in new moulds for the hi-tension lugs, making them springless and thus silent. Soon everyone wanted a 9000 kit and the belief that they were the ultimate modern recording drums gained universal acceptance.
The ‘R’ on the YD9000R title led drummers to refer to the ‘Recording’ series, although this was not officially sanctioned by Yamaha until 1985. Ever since, drummers refer to these kits loosely as ‘9000’ or ‘Recording Custom’ kits.
Perhaps the most outrageously brilliant marketing pitch regarding the Recording Custom was the way we were persuaded that birch was the ‘recording’ wood. Ironic since all those great American and UK records we worshipped had been recorded on largely mahogany (Ludwig and Slingerland) or maple (Gretsch and Rogers) tubs.
Birch, it was now pointed out, had a slightly more focused and punchy timbre than maple, which was seen as bright, and mahogany which was seen as dark. Drummers, certainly in the UK, had previously not really been aware of what woods were used in manufacture, and the RC was massively influential in bringing about this awareness.
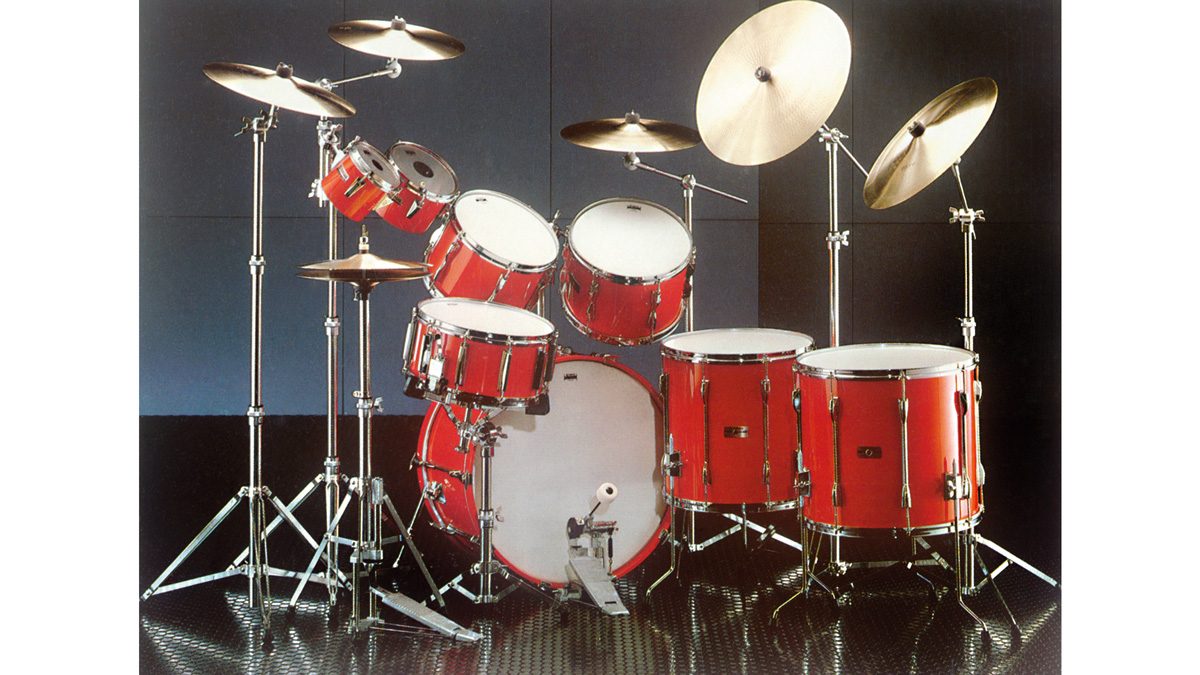
100 Years in the making
So we arrive at Yamaha’s centennial year, 1987. The company name was changed to Yamaha Corporation and the decision was made to expand the European market while reducing shipping costs.
To achieve this Yamaha took the shock step of buying the UK’s Premier drum company. As with all the Western drum companies Premier’s fortunes were rocky and Yamaha effectively saved the day by investing heavily in the Leicestershire factory.
Yamaha brought in its modern air seal and diagonal seam machinery, with two lines of moulds, trained up the workforce and set about making Yamaha drums alongside Premier’s own.
UK-built Yamahas
The first UK-made Yamahas emerged in 1989, starting with the budget Power V series, and once they had cracked that Premier took to making European versions of the Recording Custom. Later there came the birch/mahogany Rock Tour Custom series, and drums were shipped to mainland Europe, principally France and Germany.
However, sales were not as great as hoped and in 1992 Yamaha sold Premier back. The Yamaha years were undoubtedly a positive lifeline for Premier who emerged revitalised, a modern company once again.
Inevitably markets and fashions change and the Recording Custom lost its number one position in the 1990s. Where birch was the ‘in’ wood of the 1980s, maple took over in the 1990s. Yamaha moved on
to the Maple Custom, a brighter, more open sound that suited the evolving trends.
Resonance enhancement was the axiom and was accompanied by the move to small button lugs. In 1993 the mounting system was altered to accommodate the increasingly popular concept of isolation tom mounting.
This trend had started in the mid-1980s with the Purecussion rims mounting bracket and gradually every company had to come up with its own resonance-enhancing acronym. Yamaha’s solution typically involved acoustic lab research, leading to the Yamaha Enhanced Sustain System (YESS) with nodal point positioning.
The Recording Custom continued to attract customers albeit in ever-smaller numbers who wanted that legendary sound. Interest was kept alive via occasional special releases.
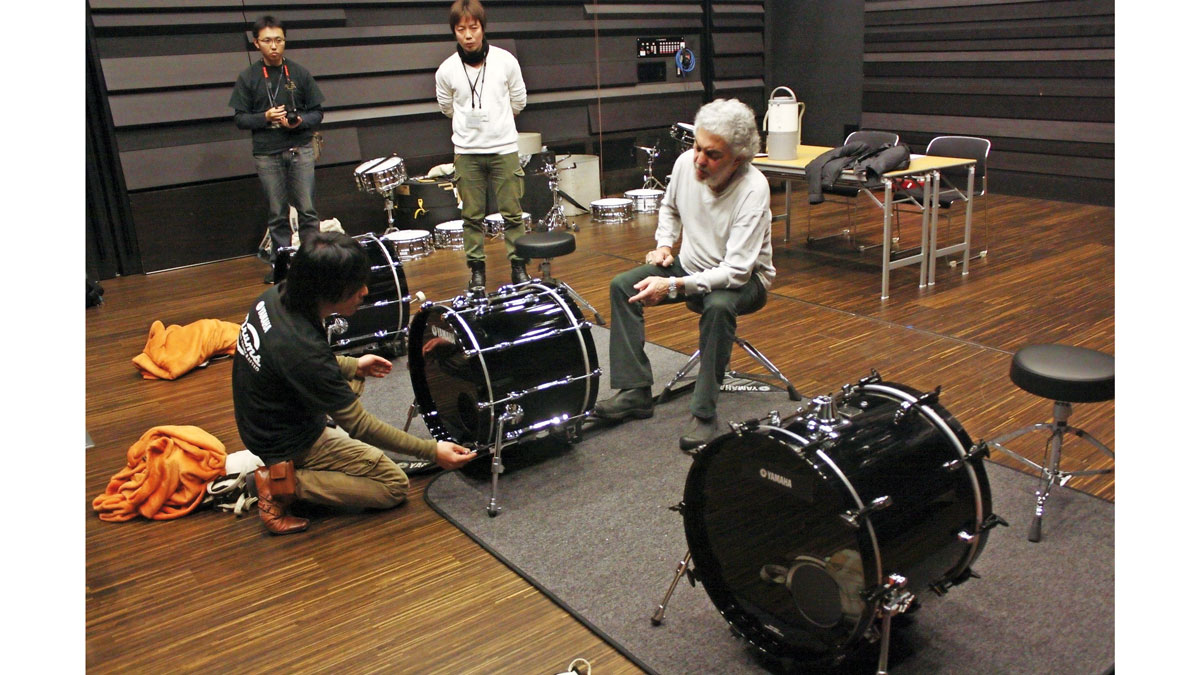
Sleeping giant
The music world was now undergoing yet another major shift with most instrument companies – both Western and Eastern – moving ever greater chunks of their manufacture to China.
In 1997 Yamaha established a new factory in Hangzhou, around 200km south-west of Shanghai in China. This facility started out producing Yamaha’s acclaimed wind and brass instruments and extensive marching percussion, although not the RC, which was still crafted in Japan.
While Yamaha continued to innovate with landmark series such as the Maple Absolute in 1998, then trailblazing beech and oak drums in the 2000s, the Recording Custom languished. In 2008 Yamaha established a custom drum factory near its headquarters in Hamamatsu, Japan, to create the ground-breaking hybrid-shell Phoenix PHX series and to further its research and development of acoustic drum kits.
Yamaha would rather its customers see its future as not so much ‘Made in Japan’, or ‘Made in China, as ‘Made in Yamaha’.
Meantime, Yamaha was slowly working towards the time when high-end drum production would be transplanted from Japan to China. The Hangzhou facility was always hi-tech and environmentally friendly and in October 2010 a similarly advanced drum factory was opened – the Hangzhou Xiaoshan Yamaha plant, representing an astonishing $10 million investment.
All professional product lines were discontinued and, in 2011, production of new high-end drum lines started in Xiaoshan, except for the PHX which continues to be built at Yamaha’s flagship workshop in Japan. Along with its in-house materials division, this workshop continues to work closely with the new factory, both facilities developing side-by-side.
As with Premier, Yamaha left all its air seal machinery with Sakae in Osaka. And Sakae, as we now know, has gone on to produce highly individual, top quality drums under its own name.
This development led to all sorts of rumours flying around a couple of years ago and Yamaha, as a major corporation, had to bite its lip, suck it up and as always let its products do the talking. But the perception that the move to China was a step down and simply a cost-cutting consideration could not be further from the truth. Yamaha would rather its customers see its future as not so much ‘Made in Japan’, or ‘Made in China, as ‘Made in Yamaha’.
Yamaha as a company always looks to the future and strives to be innovative. This was what led originally to the huge success of the Recording Custom. The substantial investment in Xiaoshan demonstrates the company’s determination to carry on in this vein. This has so far led to three new series catering for three aspects of the drummer’s needs.
First there was an update of the Oak Custom to the Live Custom, delivering a strong and warm sound from its thicker oak shells. Then in 2014 the open, expressive Absolute Hybrid Maple, with loads of innovative features and super-resonance from the YESS-III mounts. And now there’s the revised Recording Custom.
Yamaha Drums Product Manager Gavin Thomas tells us: “When we made the decision to end our current product lines it was always our intention to review and consider a new Recording Custom. We did not know what that might be, but it is the cornerstone of our heritage so we knew we wanted to give it a rebirth and not just move production – if we could prove that there was a market for it.
"The issue we had was there was such a shift towards maple products in the late ’90s and ’00s that some people thought the RC was discontinued way before it was. We were pleasantly surprised that the response when we ended RC production was strong.”
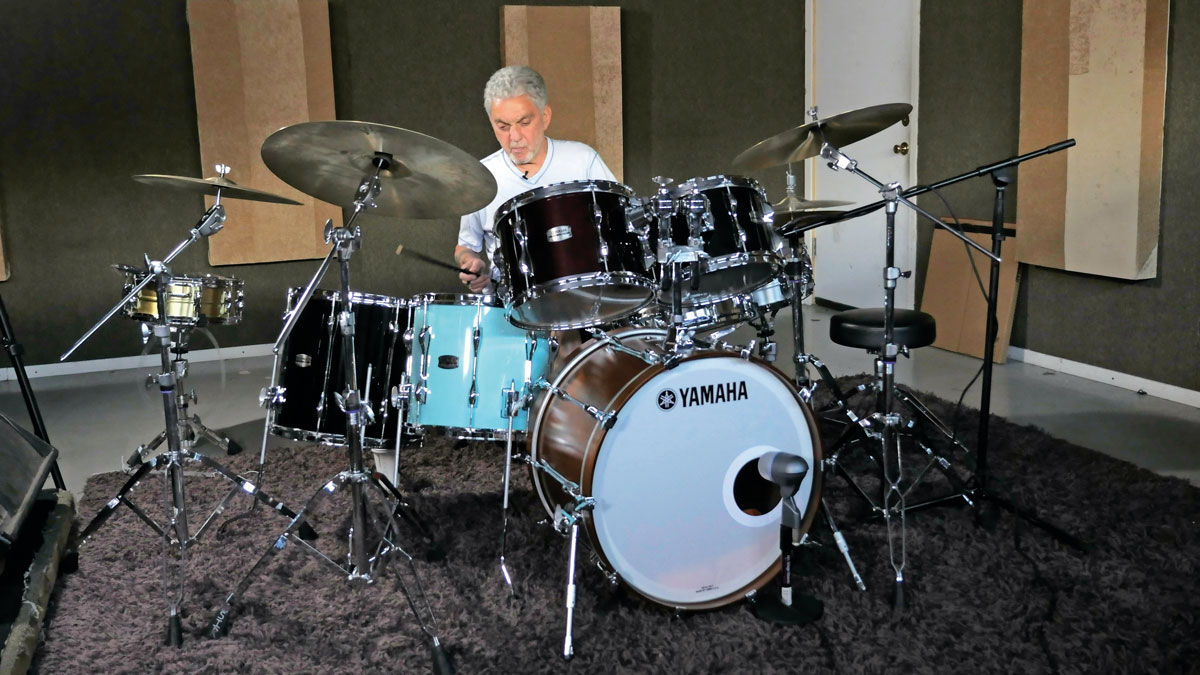
Recording Custom Sails On
Put simply, the Recording Custom was too strong a brand to dismiss. But this being Yamaha a simple reissue was not on the cards.
A deeply considered overhaul was inevitable and in fact the new RC, and a completely new collection of seven new metal-shelled snare drums, has been three years in development. Since the sound of the RC is inextricably woven in with the sound of Steve Gadd, it was decided to draw again on Steve’s thoughts, judgment and ears.
But first, in September 2012, a reliable supply of quality North American birch was secured. Yamaha assures us that this is “perfect for the target sound”, ensuring a steady continuity of supply as it replaces the vaunted Hokkaido birch of the original.
The Recording Custom was too strong a brand to dismiss. But this being Yamaha a simple reissue was not on the cards.
The drum design group, including Nori Ishimatu and Ziggy Okamoto, consulted with Gadd in August 2013 on how the drums could be improved. He had always been happy with the toms, but felt the bass drum needed more depth and roundness (he plays a maple bass drum with his own signature kit) and he was keen for the metal snare drums to be as simple and adaptable as the stock Ludwig SupraPhonics he famously played for many years.
Prototypes were knocked up and by February 2014 a second set of sample snare drums in aluminium, brass and stainless steel were prepared for evaluation by Steve while in Tokyo. Then in August of 2014 a second evaluation took place in New York involving third stage samples of six, eight and 10-ply bass drums with a variety of edge profiles and weights of lug. The third evaluation session took place in July 2015 at Steve’s home base of Phoenix, Arizona.
The outcome was to go with the thinnest six-ply bass drums but with weighted lugs and with the bearing edges changed from 45° to 30°, the resulting drums having a more powerful, rounded bass tone with a wider dynamic range. Steve also requested a new lift for the 20" bass drum which allows the pedal beater to strike at the centre giving him close to the same feel as playing a 22" drum.
The mounted toms are fitted with Yamaha’s classic YESS brackets, the same as for the past 20 years. These are not the latest YESS-III mounts employed on the Absolute Hybrid Maple. The reason is because of not wanting to over-enhance the sustain, but to retain the dry and focused sound with quicker decay, the abiding character of the 9000 series.
Yamaha is, like all companies, reliant on the fickle tastes and fashions of the drum world. But what is certain, with the impressive Chinese mega-factory backed up by the Japanese-based research lab and Yamaha’s unrivalled experience and knowledge in so many fields, Yamaha will continue to search for forward-looking solutions to drum manufacture, and offer products to delight drummers for decades to come.